Synthetic Diamonds: From Dark Industrials to Bright Gems
February 4, 2013
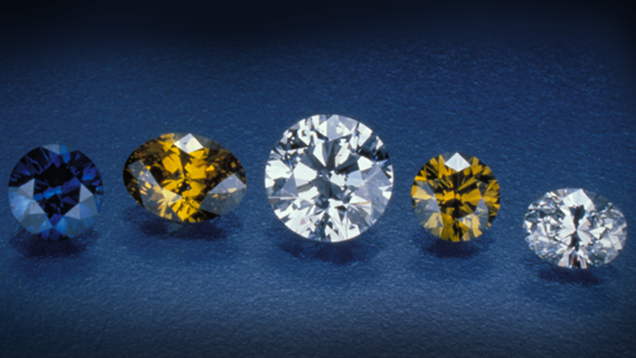
After Antoine Lavoisier discovered that diamond is a crystalline form of carbon in 1772, several 1800s-era scientists attempted to grow diamond material and made unconfirmed claims that they were successful. British writer H.G. Wells described the basic process for using high pressure and temperature (HPHT) in a 1911 story called, appropriately, “The Diamond Maker.”
It was not until the 1950s, however, that the HPHT process was used to create the first commercially viable synthetic diamonds. Today, nearly 60 years after that achievement, synthetic diamonds are making an impact in both the jewelry market and for technological applications.
In 1952, William Eversole at Union Carbide created tiny synthetic diamonds using the low pressure, comparatively low temperature, method of Chemical Vapor Deposition (CVD). A Swedish company, ASEA, successfully grew HPHT synthetic diamond in 1953, but kept their accomplishment secret. In contrast, Tracy Hall and other General Electric (GE) scientists announced in 1954 that they had discovered the correct mix of heat, pressure and carbon flux to reliably grow diamond in a laboratory.
Interestingly, these two very different methods of producing synthetic diamond were first successful within a few years of each other.
GE’s first HPHT synthetics were tiny brown diamonds that were applied to a broad range of industrial uses. Indeed, industrial diamonds were deemed so critical to the U.S. and other governments for use in manufacturing, that they amassed strategic stockpiles of them, eventually storing significant quantities of this important material.
The HPHT process essentially recreated the forces in nature that create natural diamonds – intense heat and pressure – in a growth chamber. A few years after the GE breakthrough, De Beers began to offer industrial synthetics and Russian scientists developed a diamond synthesis process all based on the same basic HPHT growth process.
While these producers manufactured millions of carats of industrial synthetic diamonds each year, none were large enough or of good enough quality for the gem industry until 1971.That’s when GE announced it had created several gem-quality synthetics and sent them to Robert Crowningshield at the GIA Laboratory for examination. The diamonds, polished by a New York diamond firm, weighed between 0.26 and 0.30 carats and ranged from J to F color. GE also created several fancy colored yellows and blues that GIA also analyzed. In all cases, the diamonds carried distinctive metallic flux inclusions that could be seen with an optical microscope, making them easily identifiable as synthetics.
The announcement sent shock waves around the diamond world, but the concern was premature. These gem-quality synthetic diamond crystals required a giant press and vast amounts of heat and pressure to produce, so they weren’t economically feasible for jewelry use.
It would be another 14 years before synthetics would become a potential issue in the diamond market. In 1985, Sumitomo Electric Industries in Japan announced that it had begun to produce gem-quality synthetic diamonds on a large scale for industrial use with updated technology from the GE process. The Sumitomo synthetics had a distinctively orange-brown or orange-yellow color resulting from the large amounts of nitrogen used to facilitate the process to grow high-quality crystals.
Sumitomo expressly denied that these synthetic diamonds were produced for the gem market, explaining that they were sold as heat conductors for electrical components. Accordingly, the company made them available only in very thin slices, unsuitable for polishing into gem-quality synthetic diamonds.
The introduction of the Sumitomo synthetics prompted GIA and De Beers into action. GIA researchers examined three Sumitomo “rough” crystals and four finished stones. They discovered that these synthetics had distinctive metal inclusions and internal growth patterns, and ultraviolet fluorescence reactions, which helped create a base of knowledge to draw on when examining future generations of HPHT synthetics.
The De Beers Research Centre outside of London began to develop a device that would enable gemological labs – and even jewelry retailers – to quickly distinguish between synthetic and natural diamond. In the mid-1990s, it reported that it had created not one, but two synthetic detection units. The smaller DiamondSure™can quickly filter the synthetics from naturals, although a small percentage require further testing. The DiamondView™, a more sophisticated unit, can detect synthetics though detailed imaging of ultraviolet fluorescence patterns using ultra-shortwave illumination.
As the technology of producing gem-quality synthetics became known, a small number of manufacturers in the U.S., China and Russia, and the Ukraine began to market them to the jewelry industry.
In the last decade, with the adaptation of the much less costly CVD growth process, synthetic diamonds much closer in appearance and quality to natural stones appeared in the gem market. This method not only functions at much lower temperatures and pressures, but also creates colorless diamonds more easily than HPHT. Most producers of large synthetic diamond crystals have been shifting to the CVD process in the past two to three years because of its lower cost. The DiamondSure flags potential synthetics while the larger DiamondView can distinguish CVD and HPHT synthetics from natural.
Despite the difference in production methods, GIA researchers using specialized equipment and methods, are able to distinguish all synthetics from natural diamonds.
Updated March 20, 2013