Visit to Chow Tai Fook
Diamond Cutting Factory in Foshan, China
January 17, 2014
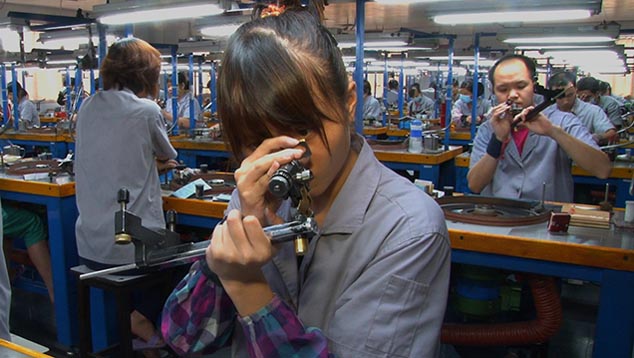
Chow Tai Fook Jewellery Group Limited had retail sales of $7.4 billion US in 2012, with a profit of $730 million. The company has been listed on the Main Board of The Stock Exchange of Hong Kong since December 2011 and it’s the world’s largest jeweler based on its market capitalization. Chow Tai Fook is a member company of the Hang Seng China 50 Index and Hang Seng Mainland 100 Index.
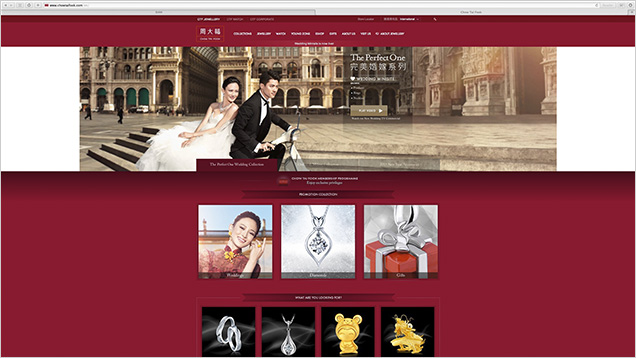
Chow Tai Fook Jewellery Group Limited is one of the best-known jewelry companies in Asia. The company is known globally for its success.
Along with its extensive retail network, the company covers the entire value chain, including raw material procurement, design, diamond cutting, jewelry manufacturing, marketing, and sales. Its principal products are mass-market and high-end luxury jewelry, including gem-set, gold, and platinum styles, and watches.Company Milestones
Chow Tai Fook had its start in the jewelry industry in 1929. In 1938 and 1939, respectively, they opened their first retail stores in Macau and Hong Kong. They introduced a line of 999.9 fine gold jewelry in 1956. This purity guarantee was highly successful at creating customer trust and building a loyal clientele.Foshan Yushunfu Jewellery and Diamond Company Limited, a then-related part of the company, opened its first diamond processing and jewelry manufacturing factory in Shunde in 1988, thereby strengthening the vertical integration of the Group's business model. Foshan Yushunfu became a full subsidiary in 2011. Zlotowski’s Diamond Cutting Works (Proprietary) Ltd., located in Johannesburg, South Africa, also became a subsidiary in 2011.
Chow Tai Fook has secured multiple sources of rough diamonds to supply their cutting factories and retail stores. In 1993, the company qualified as a Diamond Trading Company (DTC) sightholder, which gave them the right to source rough diamonds directly from the DTC. The addition of Zlotowski’s, already a DTC sightholder at the time, strengthened that position. In 2009, Chow Tai Fook became a Select Diamantaire of Rio Tinto Diamonds. In 2012, they entered into a strategic two-year agreement with Alrosa of Russia for procuring supplies of its rough diamonds.
Rio Tinto has also partnered with Chow Tai Fook to promote its Argyle mine diamonds in their stores. Rio Tinto’s new underground mining operation at Argyle has the potential to produce substantial quantities of small diamonds for the jewelry needs of the Chinese middle class.
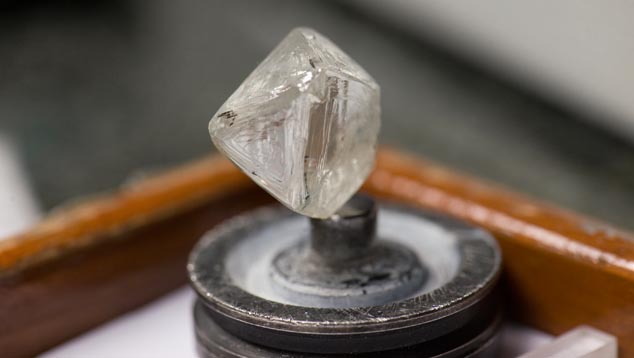
Like all diamond manufacturers, Chow Tai Fook needed to secure a constant supply of rough for their manufacturing needs in a tight global market. Photo by Eric Welch, © GIA, courtesy of Chow Tai Fook, Yueshun Fook Jewellery and Diamond Co.
In 1998, Chow Tai Fook opened the company’s first retail store in mainland China, located in Beijing. In 2003 they centralized their mainland operations with headquarters in Shenzhen. By 2010 they had 1,000 retail outlets in mainland China (including franchisees and their own outlets). Chow Tai Fook’s retail network now includes over 1,800 outlets in more than 400 cities in Greater China, Singapore, and Malaysia. It also has a growing e-commerce presence. Chow Tai Fook has plans to open 2,000 chain stores in mainland China by the year 2020. In June of 2013, during an extensive trip through China, GIA representatives visited the Chow Tai Fook diamond-cutting factory in Foshan. The team was given a highly informative guided tour of the factory, with detailed explanations of each manufacturing area and process.
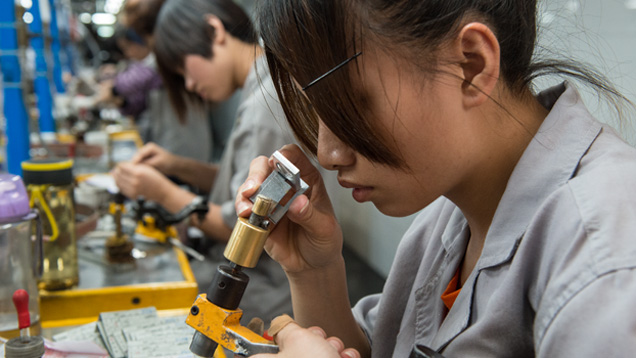
At the Chow Tai Fook factory, the GIA team extensively documented the operation of each department involved in the company’s diamond manufacturing business. Photo by Eric Welch, © GIA, courtesy of Chow Tai Fook, Yueshun Fook Jewellery and Diamond Co.
Sorting, Planning, and Marking
The tour began in the sorting, planning, and marking room. All incoming rough diamonds come to this room to be sorted by shape, size, clarity, and color. After sorting, the rough diamonds’ cuts are planned and the rough is marked. The process makes use of instrumentation that includes the Helium M Box, Sarin Galaxy 1000, and other Sarin optical measuring and marking instruments, as well as traditional hand marking.
Today, optical instruments play a critical role in planning a diamond’s cut.
The instruments can mark the rough with more precision than is possible by hand, and the line is typically straighter and more accurately placed. Even a difference of one degree, causing a weight difference of one percent, can make a substantial difference in value. This is highly important considering the tight profit margins of diamonds today and the large volumes of diamonds coming through a modern factory.Rough that requires a lot of care in the planning stages due to inclusions often goes into the Helium M Box so the planner can use a microscope to closely examine the inclusions’ nature. Included rough can also be efficiently analyzed with the Sarin Galaxy 1000, which can plan the placement of the cut stone within the rough and eliminate many of the inclusions.
The Sarin DiaMark-Z is the factory’s most commonly used optical planning and marking instrument and is used for “normal goods,” meaning stones with SI1 to IF clarity and standard sawable shapes.
The GIA team watched a planner use the DiaMark-Z to analyze and mark diamond rough for sawing. The first step was for the planner to decide what diamond shape would result in the best yield and value, based on the shape of the rough. If the rough is long, the shape of the cut stone would most likely be something like a pear or marquise.
After the cut stone’s shape is selected, the best combination of cut stone sizes is determined. For most octahedral rough, the stone is sawn off-center so one cut stone will be larger than the other. The best shape and cutting style from octahedral rough is usually the round brilliant. Some rough that is more rounded in shape might best be sawn to produce two equal-size diamonds.
The Sarin DiaMark-Z quickly displays all the potential combinations for two round brilliant cut stones, and value calculations are built into the software. A simple instrument called a polariscope uses polarized light to determine if the rough crystal contains potentially damaging strain.
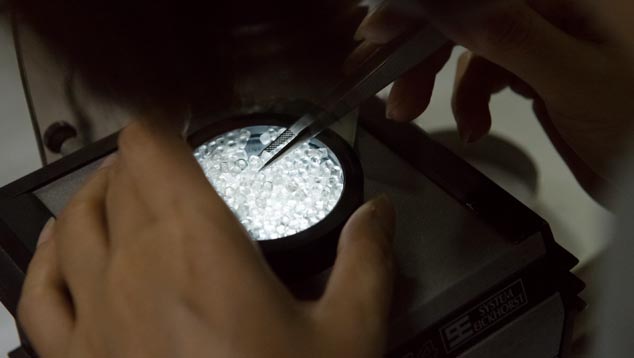
In a simple instrument called a polariscope, these diamonds are being checked for strain that could cause breakage. Photo by Eric Welch, © GIA, courtesy of Chow Tai Fook, Yueshun Fook Jewellery and Diamond Co.
The Sarin Galaxy 1000 is an accurate, automated system for mapping out inclusions in more challenging, highly included stones. This machine scans a rough diamond’s exterior and records its dimensions. Mapping of inclusions takes place inside the machine, in some cases making it difficult to see them clearly. This is especially true with the edges of very fine feathers. However, the Galaxy 1000 is much faster than the Helium M Box, which is often used for larger stones.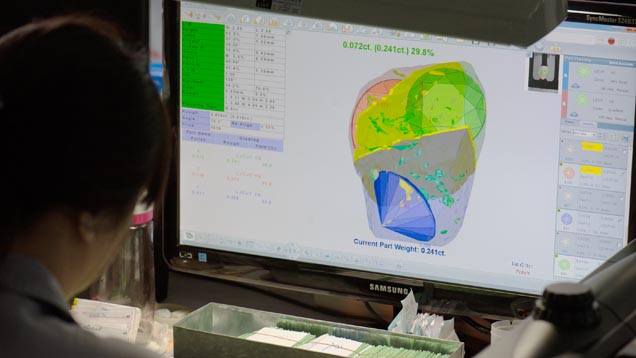
The Sarin Galaxy 1000 is a fast and efficient system for mapping a rough diamond’s inclusions. Photo by Eric Welch, © GIA, courtesy of Chow Tai Fook, Yueshun Fook Jewellery and Diamond Co.
The GIA team watched the planning of a challenging piece of rough using the Sarin Galaxy 1000 System. The instrument plotted all the inclusions and showed where round brilliants could be cut from the stone, eliminating most of the inclusions and producing higher-clarity, higher-value diamonds. The instrument identified three stones that could be cut from the rough while eliminating I1 to I3 clarity-grade inclusions. The instrument identified all the inclusions in the rough and then brought up a computer model for planning.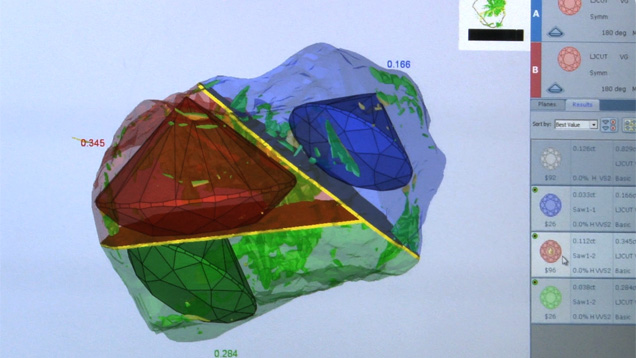
This complicated piece of rough was analyzed by the Sarin Galaxy 1000. Results showed that it could yield three diamonds while avoiding inclusions that would substantially lower value. Photo by Pedro Padua, © GIA, courtesy of Chow Tai Fook, Yueshun Fook Jewellery and Diamond Co.
Inside the Galaxy 1000, the rough diamond is immersed in a liquid, making it more transparent and allowing more accurate identification and mapping of inclusions. The rough diamond appears white and the inclusions stand out as dark, making their locations and shapes easy to see. After the scanning is complete, the files are transferred to the computer for plotting of all the inclusions onto a 3D model. The model is saved into the company’s server so the diamond markers can open the file and plan the diamond cut.
The Sarin Galaxy 1000 helps prepare rough by mapping its inclusions.
The Helium M Box works along with a scanner and a microscope. First, the scanner performs normal mapping of the rough’s outline. Next, the rough is put under the microscope and the inclusions are plotted and input through the computer. At that point, the system can plan the cut, taking into consideration the inclusions and the potential clarity grades of the cut stones.The microscope’s magnification level can reach to over 150X. The process is time consuming—one stone takes two to three hours—but the advantage is that the powerful microscope makes it very accurate, allowing for more options and the ability to improve the clarity, and ultimately the value, of the cut stones. The team watched this instrument map out a five-carat round brilliant and a four-carat round brilliant from a piece of rough, allowing for removal of a feather to improve the clarity grade of one of the cut stones.
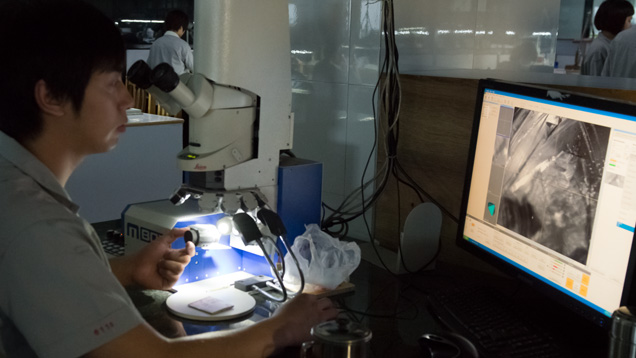
The Helium M Box uses a powerful microscope along with a scanner to locate and map inclusions. Photo by Eric Welch, © GIA, courtesy of Chow Tai Fook, Yueshun Fook Jewellery and Diamond Co.
The Helium M Box utilizes its very powerful microscope to map out the rough’s inclusions in great detail. This makes even difficult to map inclusions like fine feathers and pinpoints easier to detect. The Helium M Box is often used for analyzing larger stones. The Galaxy 1000 and the Helium M Box often work as a team. Important stones are placed in the Galaxy 1000 for initial mapping. The final mapping is done with the microscope and the Helium M Box.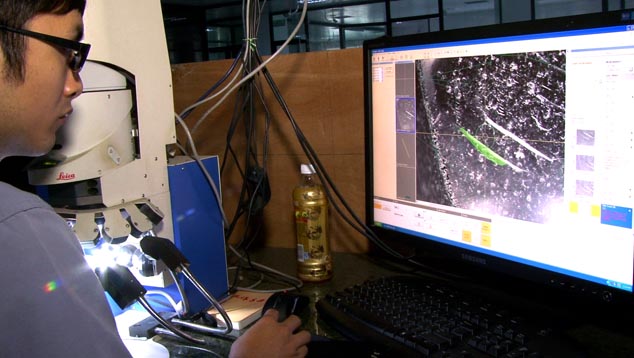
The technician used the Helium M Box and the microscope to plot a rough diamond’s surface-reaching feather, which is marked in green. Photo by Pedro Padua, © GIA, courtesy of Chow Tai Fook, Yueshun Fook Jewellery and Diamond Co.
At the end of the tour of the planning and marking area, the group’s expert guide, Simon, reviewed the machines being utilized: the Sarin DiaMark-Z, the Sarin Galaxy 1000, and the Helium M Box system. The Sarin DiaMark-Z is fast, easy to use, and accurate. It’s generally used for rough in SI1 and higher clarity grades. This instrument is not as capable as the other instruments at handling more-included rough, mapping out inclusions, or determining the cutting options for challenging rough.After sorting, planning, and marking, the information for the rough is input into Chow Tai Fook’s proprietary software system, which tracks the rough and all decisions made throughout the manufacturing process. The first information recorded is the weight of the rough and the planned weight of the cut stones. The papers holding the rough are barcoded for scanning, and have areas where all the information can be recorded as it travels through the manufacturing process. After the information is input, the rough is ready to move on to the next stage—sawing.
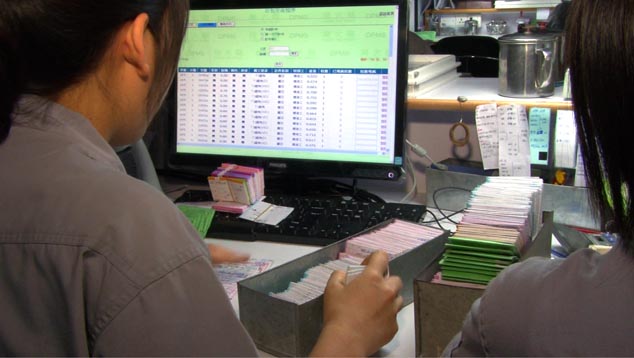
After planning and marking, it is critical to input data for tracking purposes. Photo by Pedro Padua, © GIA, courtesy of Chow Tai Fook, Yueshun Fook Jewellery and Diamond Co.
Chow Tai Fook’s software system can also track worker productivity and quality control. At every production stage, each worker’s production capacity—how many stones they can do in a day and in a week—is recorded. This information is then compiled into a graph. If any worker is not able to meet production standards, a management team works with them to determine how to raise their productivity. The tracking system is linked to the Sarin system. Salaries are linked directly to productivity.Sawing the Rough
Next, the GIA team witnessed the rough diamond sawing process. The first sawing system the team observed was the LMJ Laser Water Microjet. This advanced laser sawing process incorporates a continuous flow of water that keeps the rough diamond surface cool, helping to prevent breakage from heat. The laser beam is focused and guided into a hair-thin, low-pressure water jet to precisely target the material being sawn. The laser actually goes through the water to the diamond. This is considered an important advantage over more traditional dry lasers.
The factory uses laser technology for sawing and bruting.
Most lasers saw diamonds in a “V” shaped laser pattern. The Laser Water Microjet system uses an “I” shaped pattern with a 40-micron opening. This results in less weight loss than with the “V” shaped pattern: less than 1% for diamond rough over 1.5 carats. Simon estimated the speed of the LMJ laser to be twice that of older green-laser models, with 50% less weight loss. The “I” shaped laser pattern results in a uniform opening from the top of the cut to the bottom. The hot carbon vapor typically associated with laser diamond cutting is evacuated with the flow of water, resulting in a cleaner and smoother surfaceChow Tai Fook also makes use of green lasers for sawing diamonds. The green lasers are probably the most common lasers for sawing diamonds. They’re respected for low weight loss, minimal breakage, and production of smooth sawn surfaces. The green laser sawing machines are programmed during the day to saw multiple diamonds held in cassettes, operating all night without any employees present.
To set up the process, the technician aligns cross hairs on the sawing marks for all the diamonds in the cassette via a screen. Then the diamonds’ dimensions are programmed into the instrument’s computer, which can then saw the diamonds automatically.
Diamond sawing with both systems occurs during the normal 6-to-6 work shift. Then the green lasers are programmed to saw multiple diamonds through the night and into the next morning, when technicians pair up the sawn-off pieces and place them in the proper parcel papers.
Chow Tai Fook also uses lasers to cut the outlines of most of their fancy-shape diamonds. This process is much faster and more efficient for fancy shapes than traditional bruting methods.
Bruting and Coning
Next stop on the tour was the bruting department, where round stone shapes are created after sawing. In the bruting machine, the diamond is rotated at high speed while it’s being rubbed against a flat-surfaced wheel charged with diamond grit and water. The water keeps the heat from the friction down and lessens the chance of damage to the diamond. A one-carat stone takes about ten minutes to form, with its girdle bruted and polished. The process takes about 6 to 7 minutes for a 0.50-carat diamond and 12 to 13 minutes for a two-carat diamond.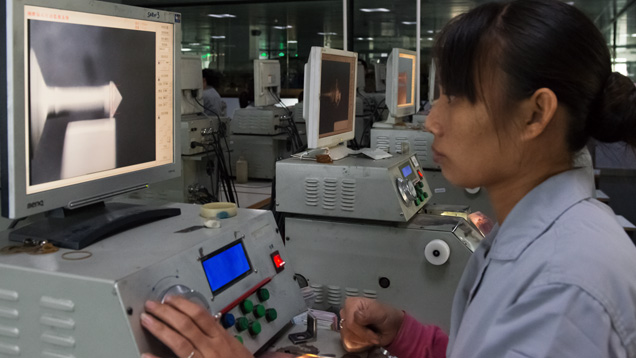
Round brilliant diamonds are bruted against spinning wheels coated with diamond grit and flowing water. Photo by Eric Welch, © GIA, courtesy of Chow Tai Fook, Yueshun Fook Jewellery and Diamond Co.
While lasers are efficient for forming fancy shapes, Chow Tai Fook does not use them for bruting round-brilliant cut diamonds. The speed is about the same for laser bruting as for bruting with diamond grit, but with laser bruting there’s more risk of stone damage.
Bruting and coning form the basic shapes of the girdle and pavilion.
After bruting forms the round shape, the next stop is the so-called coning department, where a similar process is used to create the pavilion. This process is much faster than traditional blocking.The desired pavilion angle is drawn with a red line. During the bruting of the pavilion, diamond rough is polished away until the red line is reached. This method shapes the pavilion in about 15 minutes compared to 3 hours for traditional blocking. The time needed to shape the pavilion is highly dependent upon the shape of the rough. Pavilions of fancy shapes are still blocked with a polishing wheel.
Pre-polishing Quality Control
Next, the team visited the quality control department, where the diamonds are inspected after each manufacturing stage to make sure there are no errors before continuing. This is especially important before the labor-intensive last polishing step.The different colors of the parcel papers are used to identify the suppliers, such as blue for DTC or purple for Alrosa, and also to create a visual management system. Here, the GIA team witnessed a diamond with an already-polished pavilion being checked for polish and symmetry while still in the dop.

Parcel papers are color-coded to identify the supplier. Photo by Pedro Padua, © GIA, courtesy of Chow Tai Fook, Yueshun Fook Jewellery and Diamond Co.
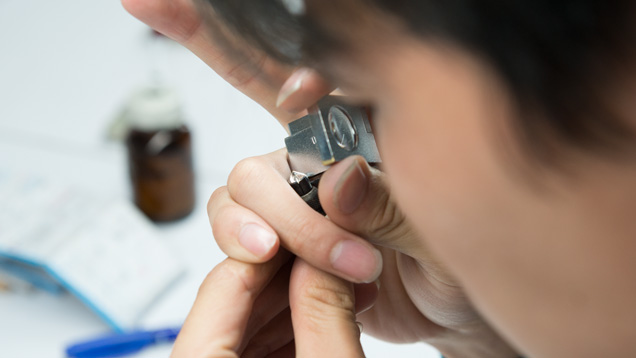
The quality of the pavilion’s polish and symmetry is carefully checked at this stage. Photo by Eric Welch, © GIA, courtesy of Chow Tai Fook, Yueshun Fook Jewellery and Diamond Co.
Polishing
In the diamond-polishing area of the factory, the team could not help but notice the polishers’ intense concentration levels. Visits to diamond-cutting factories around the world have never revealed a higher degree and intensity of focus among polishers.Demonstrating a high degree of skill and precision, the polishers constantly checked the polish and facet placement with a loupe. Throughout the polishing process, they repeatedly touched the diamond to the scaife and then quickly lifted it to check it with the loupe. For polishing the pavilion, the tang has clicks related to the pavilion facets. Each time one facet’s polish is complete, the polisher clicks to another pavilion facet. A knob on the tang allows for fine tuning of the angle. The polisher adjusts this knob constantly while checking the polish and facet placement.
The final polishing stage is a long, careful process.
The polishing speed depends on several factors, including the shape of the rough, the presence of surface graining, clarity considerations, and the shape of the finished stone. For typical octahedral, sawable rough with no complications, it takes about two hours of total polishing time—about one hour for the pavilion and about one hour for the crown—to produce a one-carat round brilliant.Final Quality Control
After polishing, all the diamonds go to the grading department for the final quality-control step. Cut is the first quality factor to be graded. Stones 30 points and above are all graded with the microscope. Stones of this size are sent to a gemological laboratory for grading reports, so it is imperative that the polish and symmetry be checked carefully before they leave the factory. Chow Tai Fook wants to make sure the cut grades they receive on reports are up to their standards and their customers’ requirements.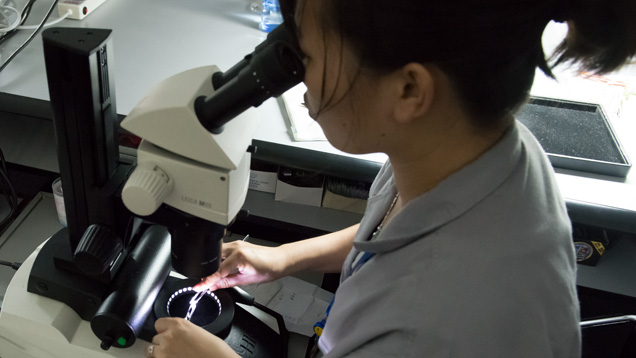
Diamonds 30 points and above are cut-graded with a microscope. For stones under 30 points, graders use a loupe. Photo by Eric Welch, © GIA, courtesy of Chow Tai Fook, Yueshun Fook Jewellery and Diamond Co.
For smaller stones, grading is done with a loupe. The grader uses a typical overhead daylight-equivalent fluorescent light and a white pad. They separate diamonds into piles based on their quality or to indicate specific re-works such as scratches on the table, polish lines, etc.After cut grading, the diamonds are color graded. Graders use daylight equivalent fluorescent overhead light, a white folded card, and masterstones. Chow Tai Fook prefers the accuracy of their graders’ eyes over any color-grading machines. By far, most of the graders are women. Chow Tai Fook has found that women tend to be more patient, focused, detail oriented, and accurate when it comes to grading.
After polishing, all diamonds go to the grading department.
The final grading step is for clarity. Like cut grading, stones 30 points and above are clarity graded with a microscope. Smaller stones are graded with a loupe. For stones under 30 points, the clarity-grading classifications are broader and not as fine. They grade these diamonds into VVS, VS, SI, and I grades without further classifying them as VVS1 or VVS2, etc. Clarity grading is very fast for these stones, with the grader grabbing a stone in the tweezers girdle to girdle for a quick look through the crown facets and then the pavilion.Conclusion
The Panyu, China, area, which includes Foshan, is known around the world as a gem cutting and jewelry manufacturing center, and with good reason. Several factors contribute to the success of the area’s industry. China markets the high quality of the country’s cutting factories in a campaign called China Cut.While labor costs are lower than in areas like Antwerp and Belgium, Chow Tai Fook reports that their polishers earn 45 percent more than those in Surat, India, and that their labor costs increase about 15 percent a year. Chow Tai Fook maintains high standards of cut quality and markets top-quality cuts globally.
With such a careful process and so many dedicated and skilled workers, it’s no wonder Chow Tai Fook is well known globally for its diamond-cutting expertise.
About the Authors
Doctor Tao Hsu is the Technical Editor of Gems & Gemology. Andrew Lucas is Manager, Field Gemology, for Content Strategy at GIA Carlsbad.
Acknowledgments
The authors would like to thank Chow Tai Fook, Yueshun Fook Jewellery and Diamond Co. diamond-cutting factory in Foshon, China. During our visit, Simon Hui and Alex Lo provided us with a very informative factory tour. Special thanks go to Nali Sha, vice president of Gems & Jewelry Trade Association of China (GAC); Ting Ding, director of National Gems & Jewelry Technology Administrative Center (NGTC) Shenzhen Lab; and Yuan Yang Cai from Chow Tai Fook, for setting up the factory tour for us. We are also very grateful to Qingyuan Yu for arranging the ground transportation for our team.