A Visit to Clarity Diamond’s CVD Facility
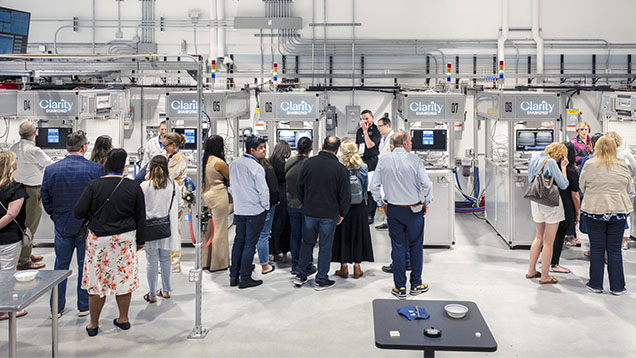
Laboratory-grown diamond sales have surged in the global gem and jewelry market over the past decade. With increased consumer demand, many in the trade are interested in learning more about these products and their supply chain. Firsthand experience, such as visiting a laboratory-grown diamond factory, helps ensure the delivery of reliable information to industry professionals and consumers.
Recently, the authors had the opportunity to visit Clarity Diamond’s facility in Austin, Texas. We first joined a group tour of around 120 attendees from the 2024 American Gemological Society Conclave (figure 1) and then returned the next day for a more in-depth visit. On both occasions, the Clarity Diamond team openly shared their knowledge of chemical vapor deposition (CVD) diamond growth techniques and products, providing visitors with a rewarding learning experience.
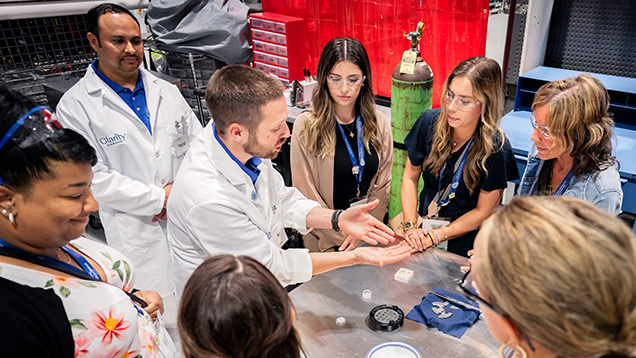
For the majority of the group, including the authors, this was their first visit to a diamond growth facility and the first opportunity to see diamonds growing in a reactor. Attendees participated in engaging demonstrations exhibiting the unique physical properties of polycrystalline CVD-grown diamond. This type of diamond is generally produced as a thin plate composed of thousands of microscopic diamonds and has many applications in other industries such as engineering and electronics. For example, one demonstration showed that polycrystalline diamond could easily cut through ice due to its high thermal conductivity (five times higher than copper), efficiently melting through it (figure 2). Many visitors commented that they wished they had this learning opportunity earlier to help them better understand CVD-grown diamonds or even diamonds in general.
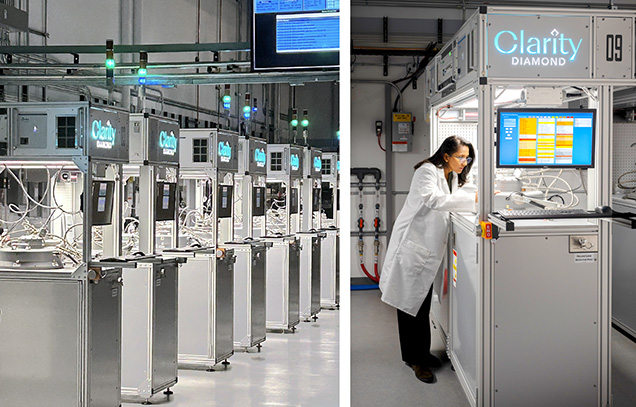
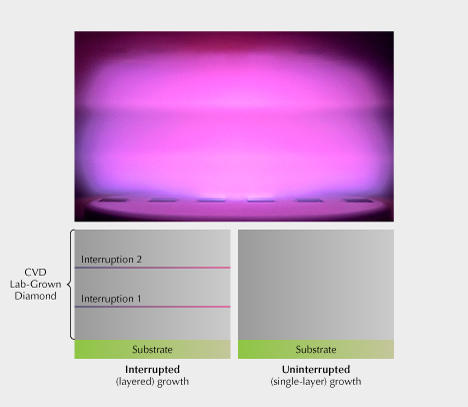
Clarity Diamond’s facility hosts a number of reactors as well as a planning and cutting area for research purposes (figure 3). A diamond seed (also referred to as a substrate), a predetermined gas mixture, and extremely hot plasma are the three necessary components to grow CVD diamonds. These diamonds can be produced with interrupted or uninterrupted growth (figure 4). The former requires the grower to remove the crystal from the reactor to polish off unwanted growth and then return it to the reactor. This procedure can be repeated many times, depending on the needs of the grower. In comparison, uninterrupted growth keeps the substrates in the reactor from beginning to end. At Clarity Diamond, the crystals are produced by one uninterrupted growth cycle. According to founder and CEO Bob Basnett, one of the main challenges in uninterrupted growth is controlling the temperature for an extended time, up to a thousand hours, which allows the crystal to grow continuously to the thickness needed.
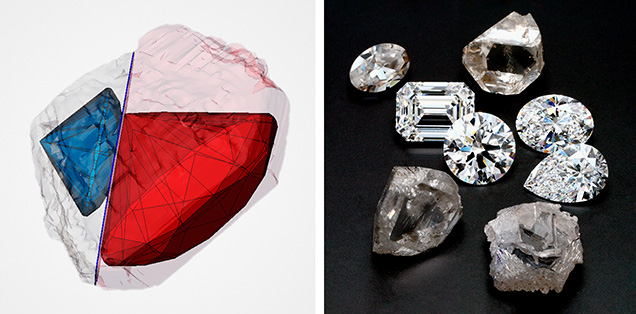
These laboratory-grown diamonds are cut and polished by Clarity’s partner, HRA Group, at their cutting factory in Ho Chi Minh City, Vietnam. Planning is done by computer-aided tools, and plans are executed following the same cutting and polishing procedures applied to natural diamonds (figure 5). HRA Group also distributes the finished products to retailers in North America, Australia, and Europe. The brand currently focuses on producing CVD-grown diamonds of high color grade (D–F) and clarity (VS2 and above).
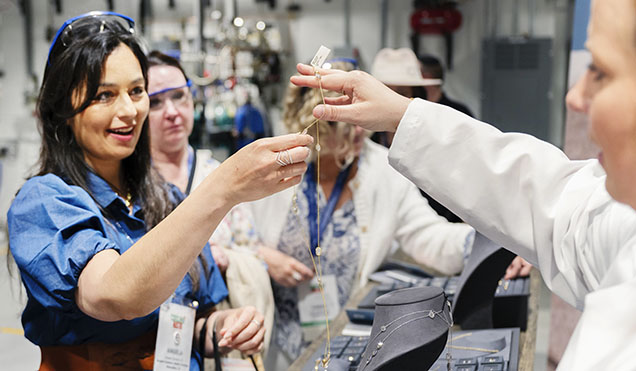
All visitors, many of whom are jewelry retailers throughout the country, had the chance to view finished jewelry mounted with CVD-grown diamonds manufactured in the facility (figure 6). This gave the retailers the opportunity to understand the product and the process behind the gem, so they can deliver accurate information to consumers. Clarity Diamond is committed to providing transparency about its growth process and business practices to retailers.
Retailer and consumer education remain at the core of our industry and GIA’s mission. Education plays an even bigger role when relatively new products are brought to the market. As GIA researchers and educators diligently keep up with new developments, we also learn from industry practitioners through opportunities such as this visit to Clarity Diamond’s CVD facility.