The Evolution of Chinese Jade Carving Craftsmanship
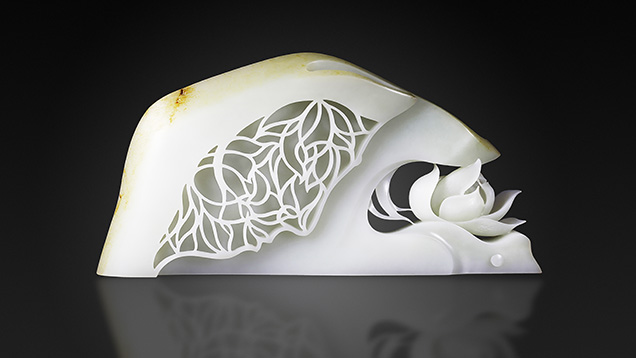
ABSTRACT
Craftsmanship is a key element in Chinese jade carving art. In recent decades, the rapid development of tools has led to numerous changes in carving technology. Scholars are increasingly focusing on the carving craft in addition to ancient designs. Five periods have previously been defined according to the evolution of tools and craftsmanship, and the representative innovations of each period are summarized in this article. Nearly 2,500 contemporary works are analyzed statistically, showing that piercing and Qiaose, a technique to take artistic advantage of jade’s naturally uneven color, are the most commonly used methods. Current mainstream techniques used in China’s jade carving industry include manual carving, computer numerical control engraving, and 3D replicate engraving. With a rich heritage and ongoing innovation in jade craftsmanship, as well as increased automation, the cultural value and creative designs are both expected to reach new heights.
INTRODUCTION
Jade carving is one of the oldest and most important art forms in China, a craft steeped in history and tradition that reflects Chinese philosophy and culture (Thomas and Lee, 1986). Carving, called Zhuo and Zhuo mo in Chinese, represents the arduous process of shaping and decorating an intractable material with abrasives to create the desired object (Hansford, 1950; Sax et al., 2004). During its more than 5,000-year history (table 1), Chinese jade carving has experienced five peaks—the late Neolithic Age (circa 3500–2070 BCE), the late Shang Dynasty (1600–1046 BCE), the Zhanguo Period (475–221 BCE), the Han Dynasty (206 BCE–220 CE), and the Qing Dynasty (1644–1911)—and was influenced by politics, economics, culture, and war (Kong, 2007). After Emperor Qianlong abdicated in 1795, the development of jade carving craftsmanship was relatively stagnant (Thomas and Lee, 1986). With the fall of the Qing Dynasty in 1911, the royal demand for jade carving faded. During that period, the folk workshops mainly focused on the carving of common jade wares such as jewelry and vessels. After 1949, state-owned jade carving factories were established one after another, with an increasing number of employees and the gradual popularization of electrically powered tools. In 1978, China opened its economy to the outside. With the support of the government, influenced by jade merchants and carvers from Taiwan and Hong Kong, and driven by an expanded domestic consumer market, China’s modern jade carving industry has seen a period of vigorous development.
There is a saying in China that “workers must first sharpen their implements when they want to do their best.” Indeed, the emergence of each peak in jade carving across its history in China is inseparable from the innovation of tools (Xu, 2011). Currently, jade carving tools are undergoing great changes, influenced by advances in manufacturing. However, little is known in the West today about the modern craft compared with ancient Chinese jade carving (Michaelson et al., 2016). Since the founding of the People’s Republic of China in 1949, papers on jade carving have been published in the West, but the majority have focused on traditional carving methods and only a few on the modern methods that emerged leading up to the 1990s (Hansford, 1950; Tucker, 1982; Markbreiter, 1985; Thomas and Lee, 1986; Desautels, 1986). In 2017–2018, nephrite jade works by Xi Yang and four other contemporary masters were collected by the British Museum for permanent display (box A), indicating that modern Chinese jade wares have begun to attract interest in the West (figure 1).
The main research factors of jade wares are texture, shape, pattern, and craft (You, 2001). Previous studies on Chinese jade carving have focused on the exploration of shapes and patterns. In recent years, with the rapid development of jade carving tools and craft, research on craftsmanship has increasingly attracted the attention of scholars (Kong, 2007; Xu, 2011). The authors of the present article conducted field visits to carving and trading sites such as Beijing, Shanghai, Suzhou, Yangzhou, Urumqi, Sihui, and Zhenping, including requisite visits to carving workshops and technical schools, to gain a more complete understanding of the current state. This article analyzes the development of jade carving tools over five periods and the representative carving craft during these periods. Finally, the processing methods and procedures of Chinese jade carving in the modern context are introduced.
EVOLUTION OF JADE CARVING TOOLS
In the process of fashioning stone tools, human ancestors gradually mastered the method of distinguishing jade from other “non-jade” stones. The emergence of the rotary machine (circa 3500 BCE), in which jade was held against a grinding tool being rotated by the other hand or another person, indicated that jade carving had completely separated from general stone craft to become an independent category (Yang, 2004, 2006). The innovation of the rotary tool is the most important factor in the development of Chinese jade carving. As the key component of the jade carving craft, the tool displays different characteristics in different development stages. Yang (2006) divided Chinese rotary machines into five generations, and Xu (2011) divided the evolution of the jade carving craft into five periods. The present authors combined the results from these studies and offer the following five generations of jade carving rotary tools in Chinese history.
First Generation (circa 3500–circa 2070 BCE). The primitive rotary jade carving machine appeared in the Hongshan and Lingjiatan cultural sites of the Neolithic Age (Yang, 2006). These jade carving tools were made primarily from natural materials such as stone, wood, and bone. Yang (1989a,b) proposed two main features of the primitive rotary carving machine. The first is that it allowed the carver to assume a sitting position. The second is that it was manually rotated.
Second Generation (circa 2070 BCE–circa sixth century BCE). The bronze rotary machine emerged and thrived from the Xia and Shang Dynasties to the early to mid-Chunqiu Period (Xu, 2014) as life in this period gradually centered on bronze technology. It is speculated that operators were kneeling and manually drove the machine to faster speeds than achievable before, based on the kneeling posture depicted in unearthed human stone carvings from this period and in the tomb of Fuhao (Yang, 2006).
Third Generation (circa sixth century BCE–circa 581 CE). The iron rotary machine appeared from the late Chunqiu Period until the Nan-bei Dynasty. Carvers still knelt on the ground while operating the machine (Xu, 2014). As smelting technology improved, iron tools were increasingly used and the jade carving machine evolved accordingly. It was still manually driven but provided increased efficiency because iron tools were sharper and more wear-resistant (Xu, 2014).
Fourth Generation (circa 581–1960). The table-type iron rotary machine was used from the Sui and Tang Dynasties through the Ming and Qing Dynasties and into the 1950s (Yang, 2006; Xu, 2014). In the Sui and Tang Dynasties, interior furniture changed people’s habit of sitting on the ground, and they instead sat on stools or chairs (Yang, 2006). As a result, the rotary machine in this period was of the table-type or tall-legged table-type and driven by a foot treadle that further increased its working efficiency (figure 2).
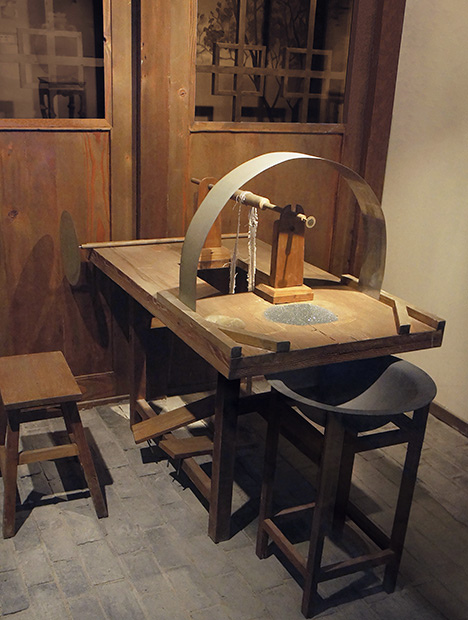
Fifth Generation (1960–present). The modern rotary machine has been used in the contemporary jade carving process since the 1960s (Yang, 2006; Xu, 2014). It was initially introduced from Europe, but with the emergence of its manufacturing industry, China began to independently research, develop, and produce these machines (Read, 1981; Markbreiter, 1985). The body of the jade rotary machine has changed from wood to iron, the grinding heads are now carborundum-coated, and foot power has been replaced by motor power (Deng, 2011; Xu, 2014). At present, there are two main types of equipment for manual carving: grinding machines and flexible-shaft machines. The grinding machine is a large apparatus, and the seated carver holds the jade while using tools of various shapes. The flexible-shaft engraving machine is small, portable, and has a handheld electric-powered rotary tool with a flexible drive (Michaelson et al., 2016), which makes it convenient to change different grinding heads (figure 3). The emergence of motor power and the improvement of tools have not only increased carving efficiency but also benefited jade carvers. The new tools are suitable for detailed ornaments and small jade wares as well as larger wares. Furthermore, motor-driven equipment has driven the introduction and refinement of tools for specific uses: for example, various types of cutters, ultrasonic drilling equipment, mechanized grinding beads, and vibratory polishers (Xu, 2014).
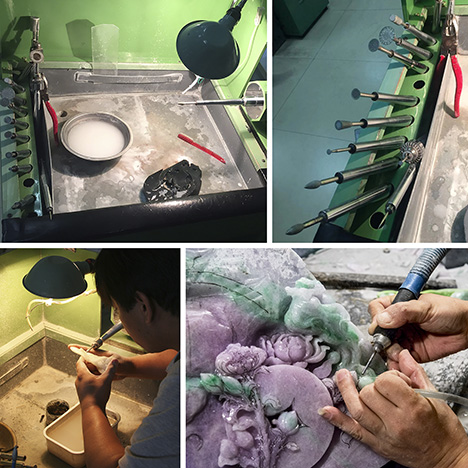
Since the 1990s, automated computer numerical control (CNC) processors have gradually been applied to jade carving. Together with design software and three-dimensional data processing, CNC engraving and milling machines can be used not only to manufacture original jade carvings but also to make 1:1 replicas of existing wares or historical relics. Three types of automated CNC engraving and milling machines are mainly used for jade carving: three-shaft, four-shaft, and five-shaft. The number of shafts represents the degree of processing freedom and in turn the quality of the resulting curved surface details. The three-shaft CNC machine is suitable for plane-relief engraving, while the four- and five-shaft CNC machines can execute three-dimensional carvings. Given cost and efficiency concerns, three- and four-shaft CNC machines are more common in the Chinese market. CNC technology can be applied to a wide range of processing types and are mainly used for engraving medium- and low-end jade and stone materials of various sizes. Its emergence and popularity means that carvings can be produced in bulk, further improving efficiency while maintaining the high intricacy of jade craftsmanship (figure 4).
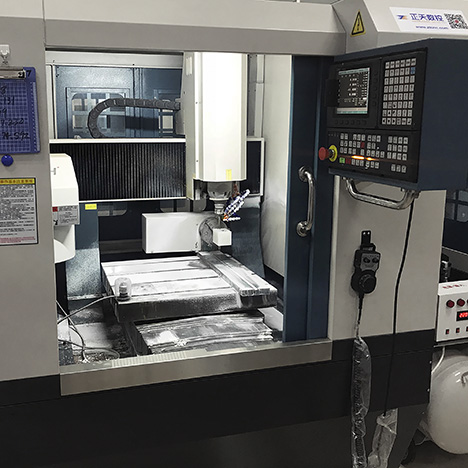
In addition to rotary tools, abrasive sands and powders are an important element in jade carving. Abrasive sands used in the primitive carving period were ordinary sands that contained a large amount of quartz particles harder than jade. With the development of jade carving craftsmanship, abrasive sands have gradually been refined (Hansford, 1950; Sax et al., 2004; Xu, 2011). Today they include natural abrasives (such as corundum, quartz, and diamond) and synthetic abrasives (such as carborundum and synthetic diamond). In general, artificial abrasives are superior to natural ones (except for natural diamond) in quality, hardness, and performance. Therefore, modern jade carving mainly utilizes artificial abrasives, which are often used for coating the grinding heads (Zhao and Zhang, 2000).
Throughout the evolution of Chinese jade carving, every tool innovation has experienced a long development cycle. The transition from the prehistoric stone tool to the bronze tool to the iron tool to the modern machine was accomplished over thousands of years. However, due to regional variations and economic constraints, new jade carving tools were not suddenly applied in a given dynasty but were gradually adopted over a longer period (Xu, 2011). For example, during the Xia and Shang Dynasties, bronze tools did not completely replace the primitive stone tools, and the two were used together for a long time (Lu et al., 2014). Nephrite, the mainstream material of Chinese jade culture, has a high toughness, which makes jade carving more difficult but promotes the innovation of tools. In early jade carving, several weeks were needed just to saw through a boulder (Hansford, 1950), making the development of tools and technology more important.
EVOLUTION OF JADE CARVING CRAFTSMANSHIP
If the tool is the fundamental force driving the evolution of jade carving, then craft is also an important factor. The two forces are inseparable. Every innovation in tools allows the carving craft to take a leap forward (Xu, 2011). Therefore, we will now analyze and summarize representative crafts used in different tool development periods (table 2).
Table 2 shows that over 5,000 years of Chinese jade culture, the development of carving tools has featured two trends: tool speed becoming increasingly faster, and grinding powder becoming increasingly harder. The evolution of tools improved processing conditions for carvers. As a result, Chinese jade carving moved toward greater diversity, complexity, and delicacy. Consider the shapes, for example. During the Xia, Shang, and Xizhou Dynasties, jade wares were mainly two-dimensional tablet shapes. With advances in tools and craftsmanship, the forms gradually became three-dimensional. In the Ming and Qing Dynasties, most jade wares displayed rounded shapes.
Although each of the five stages in table 2 corresponds to a certain historical period, any craft or technology progresses gradually through exploration and creation. The accumulation of experience takes a long time. The refinement of a craft is first tested on a small scale and then gradually promoted and popularized. Therefore, a change in dynasty does not necessarily represent the immediate progress of a craft.
Primitive Jade Carving (circa 3500–circa 2070 BCE). In the Neolithic Age, stone tools were fashioned by cutting, sanding, and drilling. These three techniques were inherited by the primitive jade carvers and further developed (Yang, 2006). Based on evidence from unearthed relics, it can be speculated that jade carving procedures in the Neolithic period mainly comprised collecting, cutting, grinding, carving, drilling, and polishing either by hand or by rotary machine. These same basic procedures were inherited by later generations. Such representative techniques as piercing, inlay, and eggshell carving (to produce thin “skins”) also made their first appearance (You, 2001; Kong, 2007; Xu, 2011). However, the quality of jade carving craftsmanship varied from place to place due to different rates of cultural development (You, 2001).
Bronze Rotary Machines (circa 2070–circa sixth century BCE). Although they emerged in the Neolithic period, inlays in the Xia, Shang, and Xizhou Dynasties outnumber those before the Xia Dynasty and display outstanding intricacy. These inlays were mainly combinations of bronze and turquoise, jade and turquoise, or bronze and jade. Jade vessels emerged in this period, with a corresponding rise in skilled hollowing (Xu, 2011).
The jade carving craft in the Shang Dynasty, which included cutting, grinding, carving, drilling, polishing, design, and shape creation, reached a high level (Technical Research Group of Beijing Jade Factory, 1976). During this dynasty, the Qiaose technique to artistically take advantage of jade’s naturally uneven or different color first appeared. In the process of Qiaose craft, the shape and placement of the colors on the rough jade should be taken into account so as to utilize the colors skillfully. The jade turtle in figure 5, unearthed at Xiaotun in Henan Province, is a successful example of Qiaose (Yang et al., 2005). Chain carving, a very difficult craft carved from a single piece of stone, also emerged in the Shang Dynasty, laying the foundation for its development in later generations (Xu, 2011).
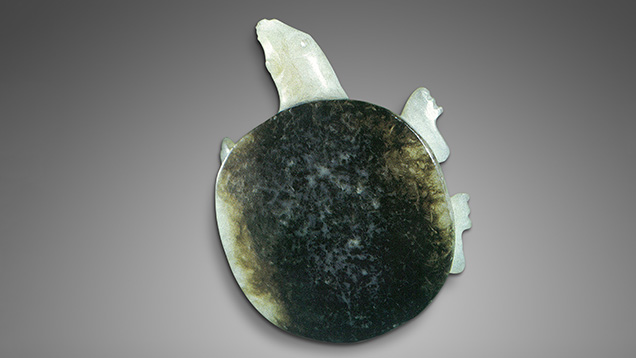
Iron Rotary Machines (circa sixth century BCE–circa 581 CE). Burial jade thrived in the Chunqiu Period and culminated in a set of special carving systems formed in the Han Dynasty. Burial jade shows no significant difference from daily jade in terms of the carving procedure but it is more concise and less exquisite (You, 2001). Take the Han Badao (concise carving) craft in the Han Dynasty as an example. Typical of burial jade, the lines from Han Badao are bold, vigorous, and concise, seemingly carved by swords (figure 6).
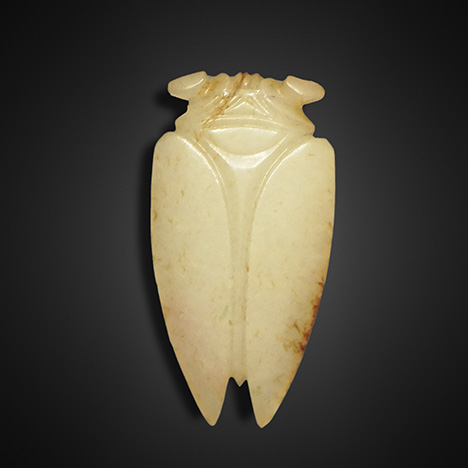
What epitomizes the craftsmanship of the Zhanguo Period is the wide application of the openwork technique (Lu and Ouyang, 2014). In this period, piercing was mainly applied to flat jade wares, but a small number of three-dimensional openwork also appeared. The craft even exerted influence during the Han and Wei Dynasties (circa 206 BCE–265 CE). Techniques integrating jade and metal, such as inlay and splicing, also surpassed those in the Shang and Xizhou Dynasties. These two techniques reached an advanced level during the Zhanguo Period, as evidenced by the number and quality of artworks applying these two crafts (Xu, 2011). Copper, silver, iron, and gold were perfectly inlaid in jade or used to stitch jade pieces together. For example, the jade clothes sewn with golden or silver thread often buried in the tombs of nobility in the Han Dynasty are elaborate and complex in craftsmanship. They are typical of splicing at this time and exemplify burial jade culture in the Han Dynasty (figure 7).
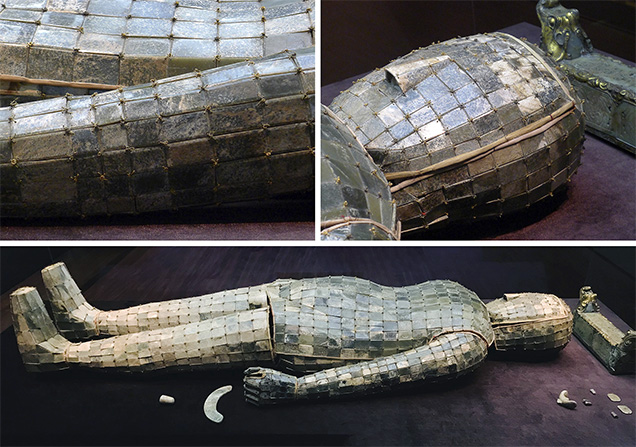
Flexible connecting, which has the same engraving principle as chain carving, was found in tombs of the Shang Dynasty but thrived and matured in the Zhanguo Period, when a great many quality artworks appeared (Xu, 2011). Among them, the sixteen-segmented jade ornament excavated from the tomb of Marquis Yi of State Zeng is the best-known application of the flexible connecting craft in this period (figure 8).
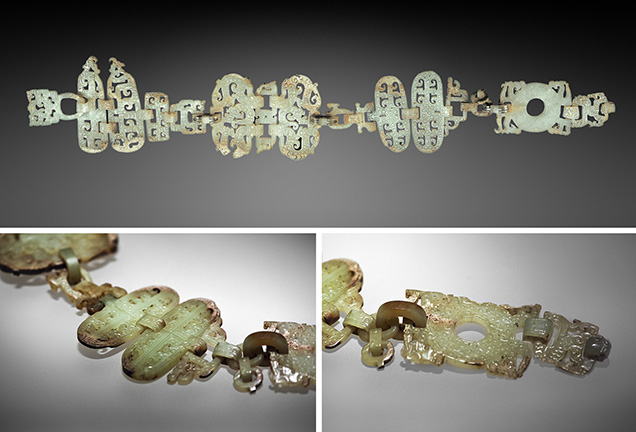
Table-Type Iron Rotary Machines (circa 581–1960). Gold and jade were already being combined prior to the Qin Dynasty (221–206 BCE), and the inlay of jade with gems and gold gained popularity during the Sui and Tang Dynasties. In the late Ming Dynasty, this craft was widely applied and became a striking feature. In the Qing Dynasty, influenced by Islamic jades that originated in central, western, and southern Asia in the late fourteenth century (figure 9), inlay often depicts various plant patterns, which gave off a sense of exotic charm (Deng, 2007; Xu, 2011).
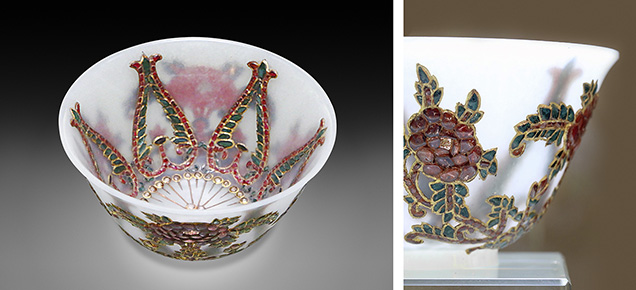
During the Song, Liao, Jin, and Yuan Dynasties (circa 960–1368), influenced by the mature arts of painting and sculpture, jade carvings became three-dimensional. Themes of human figures, flowers, animals, and landscapes were often accompanied by the distinctive openwork carving of the time. The piercing technique surged, and flat carvings were gradually replaced by three-dimensional picturesque jade wares (figure 10). In the Ming Dynasty, the intellectual “literati paintings” of southern Chinese culture, which are distinct from folk and royal paintings, highlighted romantic charms and reflected the literati’s personal feelings. This led to the incorporation of landscapes and texts in the decorative patterns of jade wares (Xu, 2011). In the Qing Dynasty, the use of royal court painters in the design of jade carvings in combination with fine craftsmanship created a peak of artistic integration (Yang, 1982; Xu, 2011).
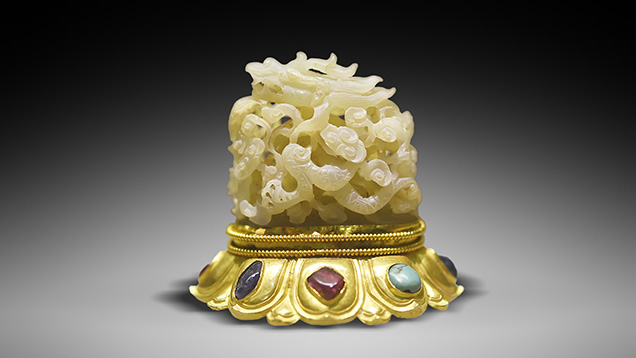
During this period, the improvement and combination of tools and craft promoted the emergence of large jade carvings (Kong, 2007). For example, the massive bowl “Dragons Amid Waves” from the Yuan Dynasty was the first large jade carving that we know of. In the Qing Dynasty, jade carvers created several large works weighing thousands of kilograms, such as the complex three-dimensional landscape (called Shan Zi in Chinese) “Emperor Yu Leading People in Subduing Floods” (figure 11) and “Nine Elders Meeting During the Huichang Period” (Xu, 2013). These large carvings are mostly themed with landscapes, human figures, and animals, often accompanied by skilled calligraphy engraving on the back or sides. To create these pieces, several jade carvers had to work at the same time in an organized fashion. Under the processing conditions of the time, such a large work would take several years to complete. Thus, the production of large jade carvings marks the peak of the craft in ancient China (Xu, 2011).
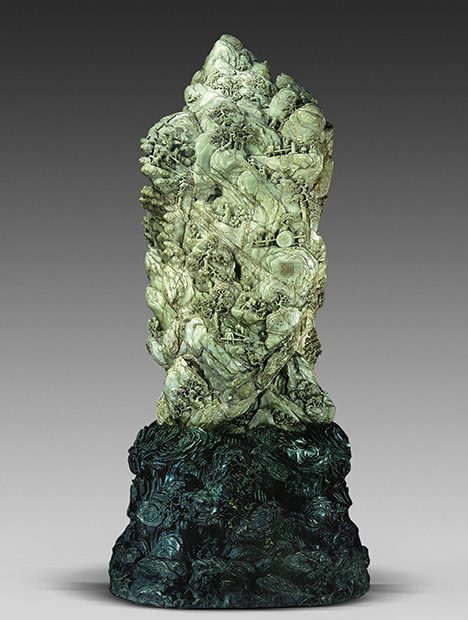
Many other techniques also emerged during this period, such as the full development of Qiaose and eggshell carving, and the emergence of jadeite carving in the Qing Dynasty (You, 2001; Kong, 2007; Xu, 2011).
Modern Machines (1960–present). After the Qing Dynasty, the traditional foot treadle was used until the early days of the People’s Republic (Xu, 2014). In the late 1950s, with the policy reform of the national planned economy, government-owned jade carving factories sprang up, led by the manufacturing centers of Beijing, Shanghai, Yangzhou, and Suzhou (Ma, 2014). Jade carvings were produced under industrial management using assembly lines (Ji, 1984). It was at this time that motor-driven carving machinery began to be employed.
With the popularization of power-driven systems in the 1960s and the continuous refinement of the tools (Xu, 2014), the modern carving industry ushered in a new era following the reform and opening up of trade in 1978. Modern tools and methods have changed jade carving, and pieces that once took years can now be finished in months or even weeks (Tucker, 1982).
Modern jade carving inherits the characteristics of craftsmanship from past dynasties (Xu, 2014) and is further developed on the basis of various ancient techniques. With the emergence of power-driven tools, jade carving has become more elaborate, with smoother lines. The common techniques of the modern craft include Qiaose, eggshell carving, piercing, chain carving, calligraphy engraving, gem embedding, gold and silver inlay, miniature carving, and others. Artisans will often make a final decision on which techniques to use based on the color, shape, and toughness of the rough and the theme of their creation. Among these techniques, Qiaose (figure 12) and piercing (figure 13) are widely used in jade carving and showcase the carvers’ creative talents. Many of these techniques are highly specialized, and as a result jade carvers often devote their whole life to one technique. Jingui Ma, for example, devoted himself to the craft of inlay with gems and gold in the way of traditional vessels and thus formed his distinctive style (figure 14).
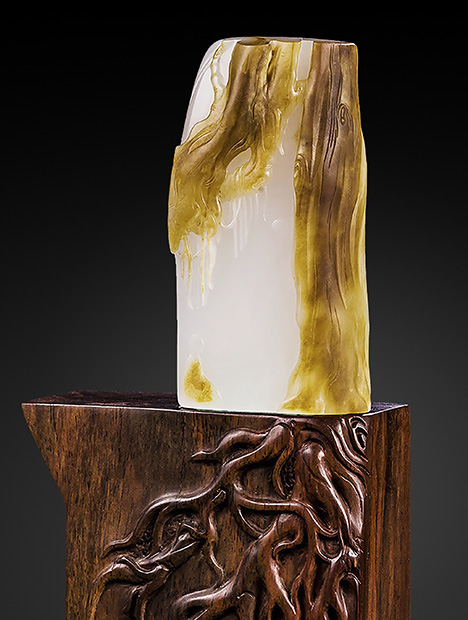
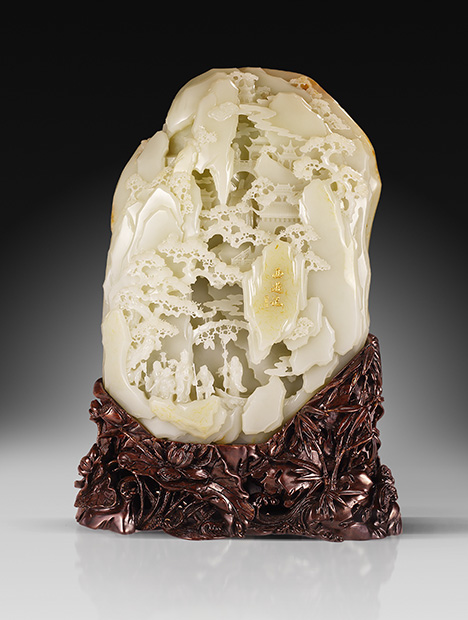
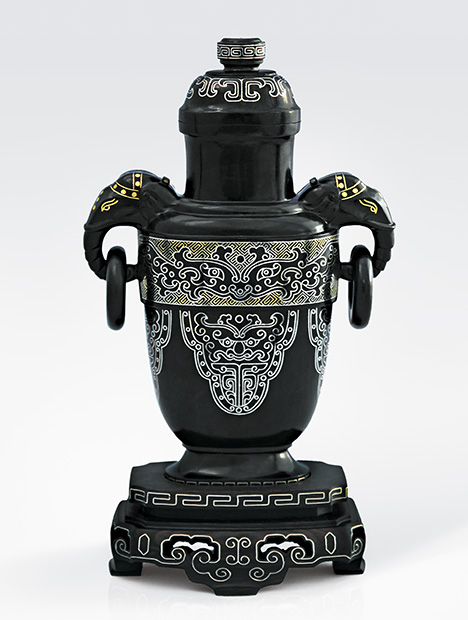
To illustrate modern jade carving, the authors statistically analyzed the 2,464 finalist works from 2012 to 2017 for the Tiangong Awards (Wang and Shi, 2020), China’s most prestigious competition. As shown in figure 15, Qiaose and piercing are the two most common, particularly the former, followed by calligraphy and chain carving. Other crafts are more specialized and mastered by only a few. Chain carving (figure 16) and eggshell carving (figure 17) are still applied mainly to vessels; calligraphy engraving rarely appears alone and is used to provide inscriptions for the jade carvings (figure 18). By and large, two or three techniques are frequently used in combination. For instance, gem embedding is usually integrated with gold and silver inlay and eggshell carving to heighten the exotic appeal (figure 19). Techniques such as 3D and relief carving are fundamental thus used in almost all pieces, which is why they are not mentioned separately in this article (Ao et al., 2012–2017).
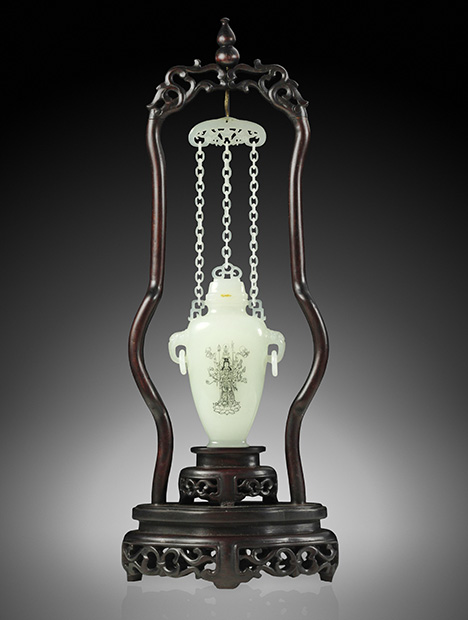
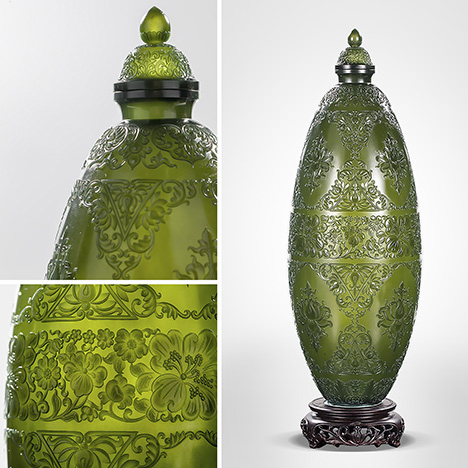
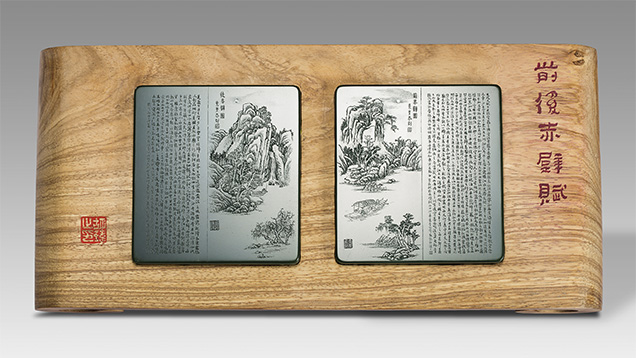
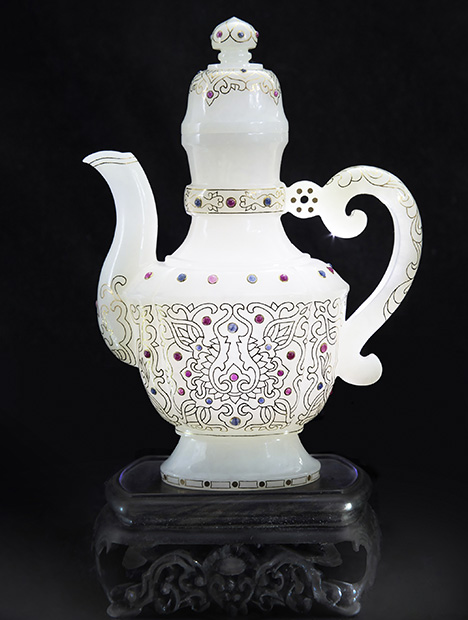
Although inheriting the ancient craftsmanship, modern jade carving attaches more importance to personal style and has made breakthroughs in expressing it with modern features. For instance, the traditional eggshell carving craft is mostly used in vessels. But master carver Xi Jiang broke tradition and carved nephrite with dark green color into wrinkled paper (Wang and Shi, 2020), which vividly shows the thinness and transparency of the work and breaks new ground for the eggshell carving technique (figure 20). Master Desheng Wu, who excels at figure carving, incorporates the concept of Western sculpture. He pays great attention to the innovation and exploration of artistic style and boldly uses exaggerated ways to endow traditional jade carving craftsmanship with modern beauty (figure 21).
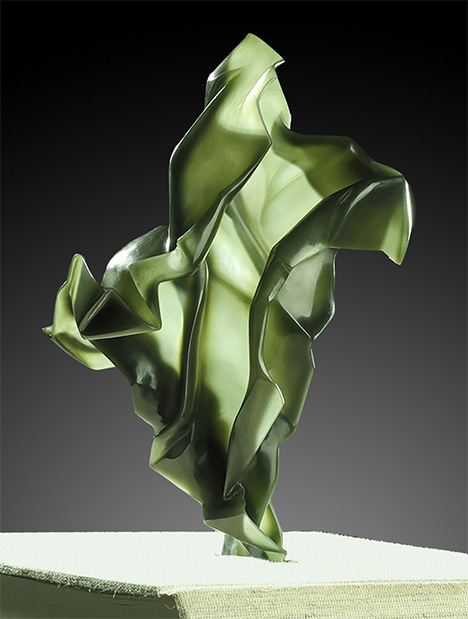
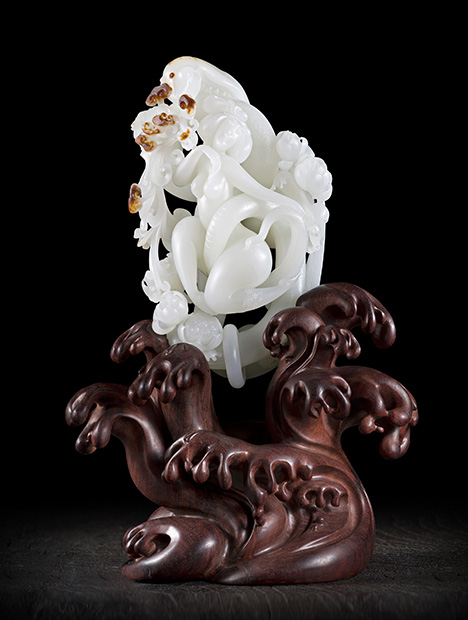
JADE CARVING PROCESS ILLUSTRATED BY MODERN WORKS
As mentioned above, ancient jade carving includes five steps: material selection, examination, design, carving with abrasives, and polishing (Xu, 2014). Depending on the tools and techniques, modern jade carving can be divided into three mainstream methods, each with a different procedure.
Power-Driven Manual Carving. This method inherited from ancient carving still enjoys a dominant role in modern China (figure 22). The procedure has remained essentially the same (Deng, 2011; Michaelson et al., 2016). Material selection and examination are targeted to maximize beauty. Design seeks to integrate the shape and patterns according to the features of the jade material (such as color and texture). Carving, usually the most time-consuming step in the process, is where design ideas turn into artwork through the use of tools. Polishing refers to the fine grinding of a jade’s surfaces to make them smooth and bright, with an aesthetic appeal. It is interesting to note that artists sometimes use different finishes (degrees of polish or lack of polish) to create stunning designs.
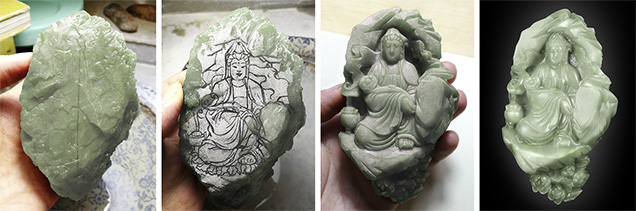
Computer Numerical Control (CNC) Engraving. This method is composed of two parts: model design and processing by machine. The model is designed using computer software. The designed model is first processed and programmed to determine the machining coordinate system and model size. The corresponding machining tools are then selected, and the program is written according to the machining requirements. In China, a CNC engraving and milling machine is frequently used in jade carving. Finally, the program is imported into the CNC machine to control its operation (figure 23).
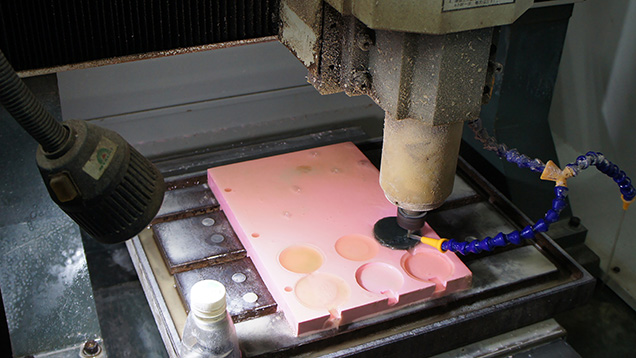
The CNC machine can achieve plane carving (figure 24) and 3D carving, but complex three-dimensional shapes and patterns can only be achieved through a combination of CNC machine and manual carving. Moreover, the CNC machine is rather limited with respect to the special techniques listed above: Only simple piercing can be achieved. The eggshell carving process has very specific requirements for jade materials, and it is difficult to use with materials with poor toughness that are prone to splitting. Qiaose, chain carving, and inlay with gold or gems rely on manual carving and cannot be achieved with the CNC machine.
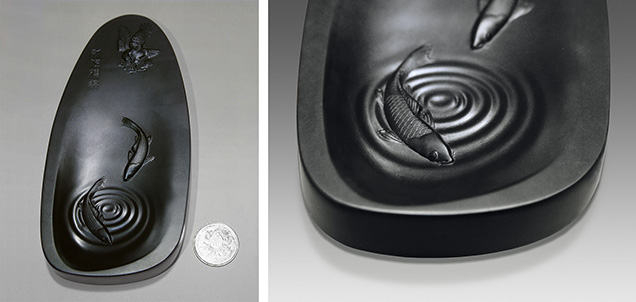
3D Scanning and Auto Carving. The first step of this method is to scan the object through the 3D scanning device, which results in a 3D model profile. The 3D model profile is then reconstructed using reverse design software to generate a new model. The coordinates of the 3D model are determined with the CNC design software, and the tool parameters are compiled into a final machining program. Under the guidance of the final program, the CNC machine tool conducts the 3D carving. This method is mostly used in the replication of ancient jade relics (figure 25).
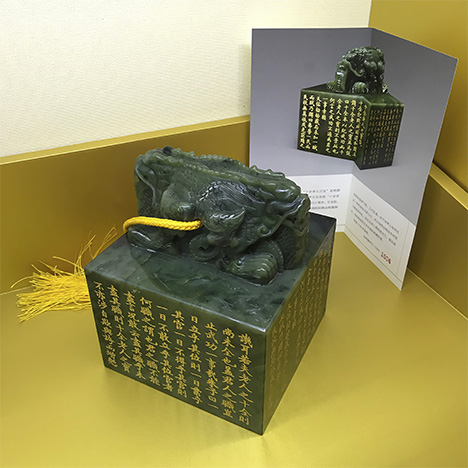
THE NATURE OF CHINESE JADE CRAFT’S EVOLUTION
You (2001) proposed that the fundamental method of studying ancient jade is to analyze it in relation to its historical and cultural background. This method applies to the study of not only ancient jade but also the modern carving craft and culture. After all, modern jade carving is integral to the history of jade. What modern power-driven implements and automated CNC engraving and milling machines are to jade carving today is no less than what iron tools are to jade carving history. Against the background of power and tool transformation, the reform and opening up of China, rapid economic development, and mass consumption, contemporary jade art demonstrates more diverse themes, more open art forms, more meticulous craftsmanship (figure 26), and a wider audience (Wang and Shi, 2020).
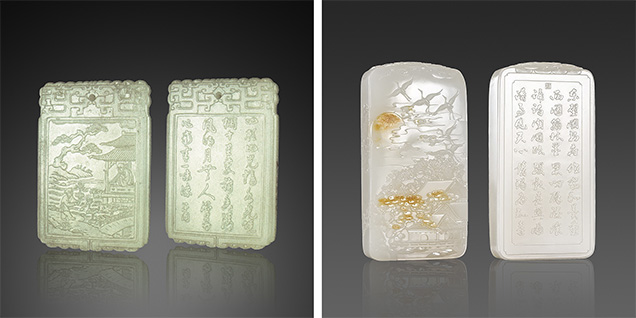
The progress of any craft or technology is a process of gradual exploration and long-term accumulation of experience (Xu, 2014). Analysis of Chinese jade carving proves a basic law—the craft learns from the past and sets a new course for the future with heritage and innovation. In general, innovation outweighs heritage. Innovation refers to multifaceted improvement and transformation based on heritage (You, 2001). Modern jade carving inherits and improves upon ancient techniques, but more importantly creates innovations in power-driven and machine engraving tools, contributing to an increase in efficiency and further development of the art. Thus, modern jade art is the best illustration of heritage and innovation working in harmony.
In Chinese jade carving, the tool plays a fundamental role and is the root of all craftsmanship transformation. Influenced by the evolution of carving tools, Chinese jade carving craftsmanship has undergone long-term transformation and still continues to develop. It has distinctive characteristics—the diversity of techniques, the gradual nature of innovation, and the adoption of foreign culture and craft (You, 2001; Kong, 2007). Thus the evolution of carving craftsmanship not only helps to clarify the development of China’s jade culture but also provides meaningful enlightenment for the growth of the modern jade carving industry.
THE FUTURE
A look at the evolution of Chinese jade carving tells us that every step forward in tools and production technology is immediately reflected in craftsmanship. In the contemporary era, the development of artificial intelligence and industrial automation will continue to boost mechanization and large-scale production in the Chinese jade carving industry. These trends will further contribute to the sustained improvement of the creative design and cultural value of jade carvings.
In this era of advanced science and technology, automated CNC engraving has become a trend, especially for middle- and low-end carvings. In the future, however, the dominant method will continue to be manual carving, especially of high-end jade wares, which represents the inheritance of 5,000-year-plus tradition. The advancement of modern jade carving can only be achieved through enhancing creativity, deeply understanding jade culture, and balancing manual and automated machine methods.