Synthetic Star Sapphires and Rubies Produced by Wiede’s Carbidwerk, Freyung, Germany
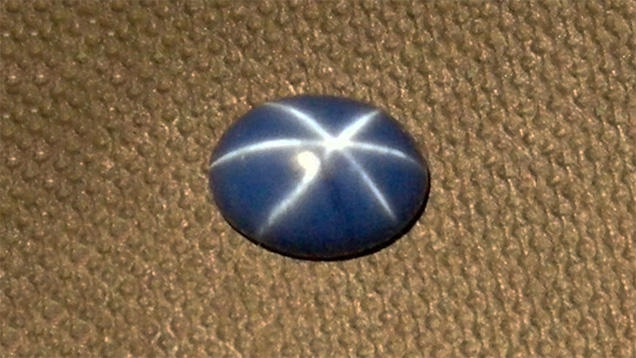
ABSTRACT
Asteriated synthetic rubies and sapphires were produced by Wiede’s Carbidwerk of Freyung, Germany, between the mid-1950s and the end of the 1970s. The rough crystals were grown slowly through a proprietary variant of the Verneuil method, developed in the mid-1950s, in the form of almost spherical to elliptical boules. After crystal growth, rutile needles were exsolved by annealing at temperatures ranging from 1100°C to 1500°C. Notably, such needles were somewhat shorter than those generally produced in asteriated material from other Verneuil manufacturers, particularly Linde in the United States, giving the cabochons a slightly different visual appearance. Furthermore, the production process using oriented seeds and a variable temperature-time protocol resulted in samples consisting of up to three growth zones. Such properties may aid in identifying Wiede’s synthetics produced up to the end of the 1970s.
INTRODUCTION
During the 1940s and 1950s, various processes for the production and/or improvement of asterism in corundum were described in patent documents assigned to Linde Air Products Company or to the Linde division of Union Carbide and Carbon Corporation in the United States. The first patent application was filed in August 1947 and published in November 1949 by Burdick and Glenn. In principle, the creation of asteriated synthetic corundum was based on a two-step process comprising (1) the production of titanium-bearing corundum crystals and (2) the formation of rutile precipitates. The precipitates were responsible for scattering and reflecting incident light and thereby forming the three intersecting light bands of a six-rayed star. The first asteriated rubies and sapphires were grown by the Verneuil technique, with the addition of a titanium-bearing compound as a component of the nutrient powder (Burdick and Glenn, 1949). The patent mentioned that the alumina powder from which the crystals were grown should contain at least 0.1% and not more than 0.3% TiO2. Without further dopants, colorless star sapphires were obtained; by including chromium oxide or iron oxide, rubies or blue sapphires could be produced.
The disadvantage of this basic process was that the resultant needle-like precipitates were confined to the skin of the Verneuil boules, thus restricting the size and number of asteriated cabochons that could be cut. Cabochons cut from the interior of the boules might not exhibit asterism, and blue sapphires could also show colorless zones in growth sectors without titanium. Furthermore, cabochons cut with the titanium-bearing skin in the center of the final cabochon might not display asterism on the sides toward the base (Burdick and Jones, 1954).
To overcome these disadvantages and grow rubies and sapphires with more complete stars—and without colorless zones in blue sapphires—it was necessary to have a more homogeneous distribution of titanium in the corundum crystals. Obtaining such an improved distribution was accomplished by growing the Verneuil boules under fluctuating thermal conditions. In practice, this fluctuation was achieved by alternately increasing and decreasing the rate of oxygen fed to the oxygen-hydrogen flame of the Verneuil burner. The process mentioned was patented in United States by Linde (Burdick and Jones, 1954), and a series of international applications were also filed (e.g., in Germany, Great Britain, France, and Switzerland). As represented schematically in the patent by Burdick and Jones, the sapphire and ruby boules grown under such conditions showed—in the direction of crystal growth—layers with high titanium contents in all zones, alternating with layers where titanium was restricted to the rim of the boules. Again, the concentration of titanium oxide within the alumina powder used for crystal growth was stated to be in the range of 0.1 to 0.3 wt.% TiO2.
As a consequence of the protections against possible infringement afforded by the patent filings, other producers who wished to use the Verneuil process for growing gem-quality asteriated rubies and sapphires had to develop techniques different from that described in the Burdick and Jones patent. In particular, German researchers were successful in independently developing such a method. Synthetic asteriated corundum of German production began reaching the market in increasing quantities in the second half of the 1950s, and the material was described as contrasting with the Linde stones in both visual appearance and gemological properties (Breebaart, 1957).
The German synthetic star rubies and sapphires (figure 1) were grown by Wiede’s Carbidwerk of Freyung, Bavaria, a family-owned company that had been creating rubies, sapphires, and variously colored spinels since about 1913 (Schmetzer et al., 2015). The technical differences between the German and American production processes were divulged in German patents DE 1 002 300 and DE 1 007 753 by Ancot and Eppler, both filed in February 1955 and then published in August and October 1957, respectively. Descriptions of the new asteriated gem corundum were also provided in gemological publications by Eppler (1957/1958, 1958 a,b). While these mentioned that a slower growth process was used in Germany, the emphasis was on contrasts in the gemological properties and visual appearance of the star rubies and sapphires produced by Linde and at Wiede’s. The publications did not refer to the underlying patents or production methods that resulted in such differences between the two companies’ materials.
The synthetic star rubies and sapphires produced by Wiede’s Carbidwerk have similarly been mentioned in gemological textbooks covering asteriated corundum (e.g., Nassau, 1980; Hughes, 1997, 2017), but, again, details of the technology were neither given nor associated with properties of the samples. The present paper thus focuses on further closing the gap in the gemological literature regarding historical production processes for synthetic gem materials.
TECHNICAL INFORMATION DISCLOSED IN PATENT DOCUMENTS
The methods described by Ancot and Eppler (1957 a,b) in the patents cited above and assigned to Wiede’s Carbidwerk were applied for the production of asteriated rubies and sapphires from the mid-1950s to the end of the 1970s. Later production methods for asteriated corundum at Wiede’s no longer employed these specific techniques, primarily for economic reasons (H. Schulz, pers. comm., 2014).
Both patent documents indicated that a better distribution of titanium throughout the complete Verneuil-grown corundum crystal was achieved if the TiO2 content within the Al2O3 nutrient powder was increased beyond the 0.1% to 0.3% range described in the patents assigned to Linde. Specifically, Ancot and Eppler quoted a percentage of up to 0.52% TiO2. The titanium oxide was preferably added in the form of anatase. Without other modifications to the growth method, however, the titanium-enriched synthetic material so obtained was highly fragile. To overcome that problem, the melting time for production of the corundum boules was increased by at least a factor of two, or better yet by a factor of six. This, in turn, could be accomplished by decreasing the rate of powder fed per time unit to the growing surface of the crystal in the Verneuil burner.
In the temperature-time protocol applied for crystal growth, the temperature of the Verneuil flame was progressively increased during the initial phase of the production period by altering the oxygen-hydrogen ratio. The mixture of gases started at an O2:H2 ratio of 40:100 and was slowly changed to a ratio of 49:100 by the end of this first stage in the growth process. After the maximum O2:H2 ratio had been reached, further growth of the ruby or sapphire crystal during a second phase was performed while sustaining the high flame temperature at a constant level.
The resulting rough product did not take the typical form of a cylindrical boule; rather, the product was an almost spherical or elliptical corundum crystal (figure 2, left). The corundum sphere had relatively low internal tension, thus eliminating the normal stress-induced need for splitting cylindrical boules along their longitudinal axis. Rutile precipitates, which were obtained by exsolution in a subsequent heat-treatment step between 1100 and 1500°C using the classical annealing process described in the patents assigned to Linde (see above), were in general equally distributed throughout the ruby or sapphire spheres.
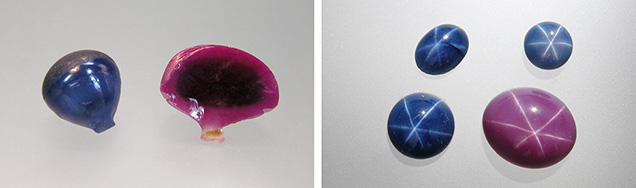
As an example, the production time (melting time) for a spherical corundum crystal of 13 mm in diameter has been quoted at 166 minutes. During the first phase of production, while the mixture of gases was being progressively altered, a spherical boule with a diameter of 10 mm could be obtained in a period of 85 minutes. During the second stage, performed while the high flame temperature was maintained, the diameter could be increased from 10 to 13 mm over a period of 81 minutes. In typical practice, only a single asteriated cabochon would be cut from such a heat-treated, rutile-bearing spherical to elliptical ruby or sapphire crystal (H. Schulz, pers. comm., 2014).
MATERIALS AND METHODS
To prevent any potential confusion with synthetic asteriated gem materials manufactured by Linde or any other producer, the present study started with samples obtained directly from Wiede’s Carbidwerk. One synthetic blue sapphire boule, one sapphire cabochon, and one ruby cabochon were furnished by the producer in Freyung. All three samples had unquestionably been manufactured by the general method described in the patents cited above. Four Wiede’s synthetic ruby boules from the Mineralogische Staatssammlung (Bavarian State Collection for Mineralogy), Munich, were made available as well. These samples most likely had been donated by Eppler, who also served as a professor teaching mineralogy and gemology at the University of Munich. One additional ruby and three sapphire cabochons with similar properties were provided from two private collections in Germany and Austria. In summary, we were able to examine one sapphire and four ruby boules and four sapphire and two ruby cabochons (figure 2).
All samples were inspected visually and microscopically, especially in immersion. For maximum visibility in evaluating growth zoning and the sizes of rutile needles, one slab was sawn from the base of the blue asteriated cabochon obtained directly from the producer (figure 1) and then polished. To resolve acicular inclusions, this slice and the bases and domes of all six cabochons were also examined at higher magnification (up to 1000×) than normally applied in gemology, in reflected and transmitted light, using a Leitz Ortholux II Pol-BK or a Leica DM LM polarizing microscope. Because the needles observed optically were of different sizes and extremely small in one sample, micro-Raman spectroscopy of four ruby and sapphire cabochons was performed with a focused as well as a defocused primary laser beam using a Horiba XploRA confocal Raman microscope with a 532 nm laser.
VISUAL APPEARANCE AND MICROSCOPIC FEATURES
The external shape of the five rough samples showed that crystal growth had initiated at a small colorless shaft and then gradually widened to larger diameters. The resulting synthetic ruby or sapphire crystals exhibited slightly flattened to slightly elongated (elliptical) or almost spherical forms (figures 3 and 4). As proven by the pleochroism of the crystals, the c-axis of the samples was parallel to the direction of crystal growth. Internal growth zoning in the form of sequential curved layers was observed (figure 4, center), especially in some of the ruby crystals that had been split in half (figure 3). These split boules offered a clear visual demonstration of the shell-like internal structure.
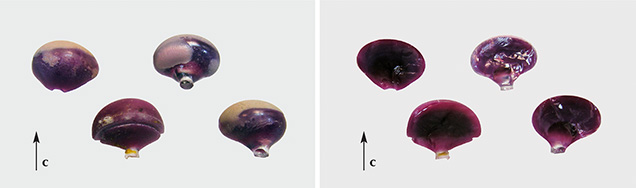
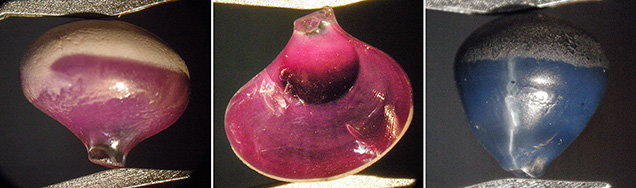
With regard to coloration and diaphaneity, three of the four sapphires and both rubies showed a distinct zoning when viewed toward the base of the cabochons, with a clear blue or red center and a somewhat milky bluish or reddish rim (figure 5). Such zoning was apparent when an almost spherical ruby or sapphire boule had been cut at or close to the largest diameter of the crystal (again, see figure 4, left and center). A “W” had been inscribed by sandblasting on the back of one of the cabochons to designate the producer (figure 5, right), a practice used for some of Wiede’s asteriated stones (H. Schulz, pers. comm., 2014).
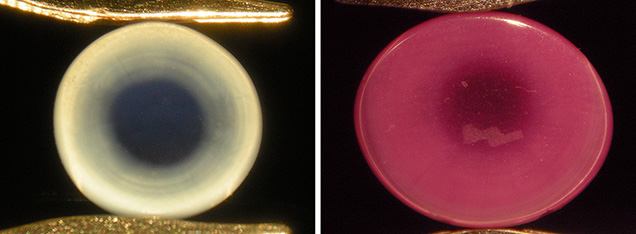
Conversely, any similarly clear central areas, if extant, were obscured in the rough samples. The rough crystals were principally opaque, appearing slightly translucent at best, due to a high concentration of gas bubbles. This was particularly evident throughout the larger, core regions of the crystals, with only the outermost layers of certain ruby samples showing slightly higher transparency than the central portions (again, see figure 3). For cut samples, in contrast to the rough material, three of the four examined sapphire cabochons and one ruby showed an outermost layer with higher transparency than observed for the main body of the samples. This was best seen in immersion (figure 6, A and B), which clearly revealed a shell-like, layered structure, with different layers containing different concentrations of gas bubbles (figures 6, B–D and 7, left). At higher magnification, the gas bubbles appeared nearly round (figure 7, center and right).
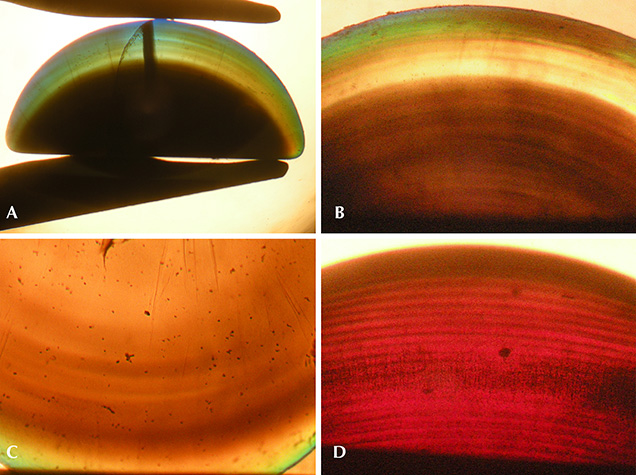
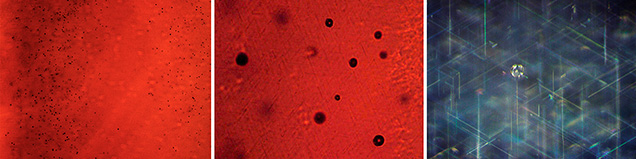
In addition, the samples showed irregularly shaped grain boundaries that crossed the arms of the six-rayed star (figure 8, left). These grain boundaries (also designated as low-angle grain boundaries) could likewise be seen in immersion in transmitted light, together with prismatic glide planes (figure 8, right), the latter of which are referred to as “Plato” striations in the gemological literature. Higher magnification revealed that the grain boundaries (figure 9, left) were related to internal stress (figure 9, center) and that prismatic glide planes were mostly developed at the rim of the sample, forming angles of 120° with each other (figure 9, right). The nature of glide planes is discussed briefly in box A.
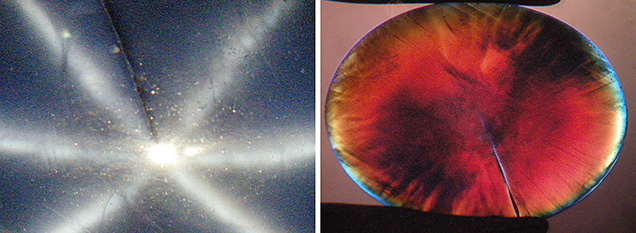
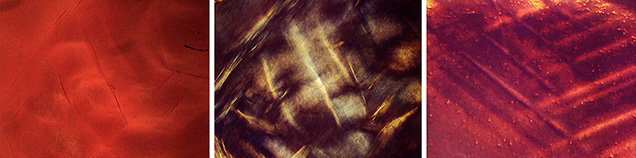
Box A: Orientation of Rutile Needles and Nature of Plato Lines in Synthetic Corundum |
Plato lines are a characteristic feature of Verneuil-grown synthetic corundum. The observed pattern, in most cases consisting of two or even three series of intersecting structural planes, is best seen under crossed polarizers in a direction of view parallel to the optic axis of the ruby or sapphire (Plato, 1952, 1952/1953; Müller, 1952). In gemological textbooks, the description of Plato lines in synthetic corundum is occasionally associated with twinning, repeated twinning, or glide twinning parallel to hexagonal prism faces (Hughes, 1997, 2017). Similarly, Eppler (1964 a,b) identified the pattern as polysynthetic twinning parallel to the first-order hexagonal prism m {1010}. In doing so, he cited a previous, more detailed publication in Deutsche Goldschmiede-Zeitung. Unfortunately, the date of this prior work was given erroneously as 1956 in Eppler (1964a), requiring reference to Eppler (1964b), in German, to ascertain the correct 1959 date. In that earlier publication, Eppler (1959) recounted investigations of Plato striations in synthetic asteriated Verneuil-grown corundum. He offered details of etching patterns seen in synthetic corundum and described experiments to examine the orientation of rutile precipitates and Plato lines. He observed that the elongation of the exsolved rutile needles was parallel to the planes of the Plato pattern and, further, concluded that the rutile needles and the planes of the Plato pattern were parallel to the first-order hexagonal prism m {1010}. This conclusion was based on Eppler’s awareness of the fact that the second-order hexagonal prism a {1120} in the crystal class of corundum is parallel to a mirror plane, and thus a cannot be considered a twin plane (figure A-1). ![]() Figure A-1. Schematic representation of crystal faces (top) and crystallographic directions (bottom) in the crystal class of corundum, D3d, with a view parallel to the c-axis. Symmetry elements depicted include the three-fold axis seen in the center and the mirror planes represented by white lines (two-fold axes are not given for simplicity). The first-order hexagonal prism {1010} is indicated by the symbol m and the second-order hexagonal prism {1120} by the symbol a. The second-order prism faces a are parallel to mirror planes and parallel to the <1010> directions.
In contrast, it is generally known to gemologists that rutile needles in natural asteriated and non-asteriated rubies or sapphires are located in planes parallel to the basal pinacoid (0001) and oriented parallel to growth planes representing the second-order hexagonal prism faces a {1120} of the host (Weibel, 1985; Hughes, 1997, 2017). In cross sections parallel to the basal pinacoid, growth zoning parallel to the second-order hexagonal prism a {1120} appears visually identical to growth zoning parallel to second-order hexagonal dipyramids—e.g., n {2243}, w {1121}, v {4483}, or z {2241}. Natural corundum from certain occurrences, such as basaltic sapphires from Australia, Madagascar, or Thailand, show mostly hexagonal dipyramids and no hexagonal prism faces. Consequently, in cross sections perpendicular to the c-axis, rutile needles appear either parallel to traces of the second-order hexagonal prism or parallel to traces of any of the hexagonal dipyramids.The same orientation of inclusions holds true for synthetic corundum that contains three series of elongated rutile or TiO2 particles on planes parallel to the basal face (0001) of the host crystal. The orientation of these needles, which are also frequently twinned, is typically identified (for instance by electron diffraction) as being parallel to the <1010> direction of the host, which is parallel to the second-order hexagonal prism a {1120} (Bratton, 1971; Busovne et al., 1979; Philips et al., 1980; Moon and Philips, 1991; Viti and Ferrari, 2006; He et al., 2011). Relevant orientations of crystal planes and crystallographic directions are depicted in figure A-1. Although Hughes (1997, pp. 156–158, and 2017, p. 270) would appear to mention one exception to the foregoing well-established orientation scheme for rutile or other TiO2 precipitates in synthetic corundum, he cited in support Takubo et al. (1980). That study, in turn, characterized the orientation of rutile needles as parallel to the <1010> direction of the host. The implication is thus that Hughes (1997, 2017) mistakenly conflated crystallographic directions and crystal faces (again, see figure A-1). Corundum specimens that were deformed by the application of stress show various slip systems. The main types of plastic deformation are described in the literature as basal and prismatic slip, caused by basal glide planes parallel to the basal pinacoid c (0001) and by prismatic glide planes parallel to the second-order hexagonal prism a {1120} (figure A-2). Occasionally, the presence of a rhombohedral slip system is discussed as well (Scheuplein and Gibbs, 1960; Stephens and Alford, 1964; Klassen-Neklyudova et al., 1970; Gooch and Groves, 1972, 1973; Snow and Heuer, 1973; Bilde-Sørensen et al., 1976, 1996; Kotchik and Tressler, 1980). More specifically, basal and prismatic glide systems are characterized by the glide plane and the glide direction: |
Figure A-2. Schematic representation of prismatic (left) and basal (right) glide planes in corundum. First-order hexagonal prism faces {1010} are indicated by the symbol m, second-order hexagonal prism faces {1120} by the symbol a, and basal faces (0001) by the symbol c. Glide planes (yellow) are parallel to a or c planes, and the glide directions are shown by arrows.
|
prismatic slip system: glide plane a {1120}, glide direction <1010> Basal and rhombohedral glide systems may also be confined to rhombohedral or basal twinning (Heuer, 1966; Wang and Mikkola, 1992; Lagerlöf et al., 1994). However, due to the fact that the second-order hexagonal prism in corundum (crystal class D3d) is parallel to a mirror plane, this glide plane is not considered a twin plane. Conversely, the first-order hexagonal prism m {1010} is not parallel to a mirror plane. As a consequence, a plane parallel to the first-order hexagonal prism may exist as a twin plane in corundum, as described for flux-grown Chatham synthetic sapphire (Schmetzer, 1987; Kiefert and Schmetzer, 1988). In summary, we conclude that rutile or other TiO2 needles in natural or synthetic corundum are located in the basal plane and form three series of oriented particles parallel to the second-order hexagonal prism a {1120}, which is equivalent to the three <1010> directions. The second-order hexagonal prism constitutes one of the principal systems of plastic deformation in corundum but is not considered a twin plane, due to the presence of mirror planes parallel to this face in the applicable crystal class. Plato lines seen in Verneuil-grown synthetic corundum thus represent glide planes resulting from plastic deformation caused by internal stress. Consequently, the term “glide twinning” is erroneous and should not be used. |
RUTILE NEEDLES
In the synthetic blue sapphires and rubies produced by Wiede’s Carbidwerk, three series of needle-like precipitates, forming angles of 60° with each other, were visible at high magnification (figure 10, A–C). Knee-shaped and V-shaped twins were seen occasionally. Raman spectroscopy of the four Wiede’s cabochons examined—which, as noted previously, was performed with both focused and defocused laser beams because of the small thickness of some needles—yielded the lines of the corundum host, together with the strongest lines for rutile. Fixing the sample under investigation and observing it at different magnifications, we determined that the elongation of the rutile needles was parallel to the prismatic glide planes (Plato striations). This indicated that both the rutile precipitates and the glide planes were oriented parallel to the second-order hexagonal prism (for further details, see again box A).
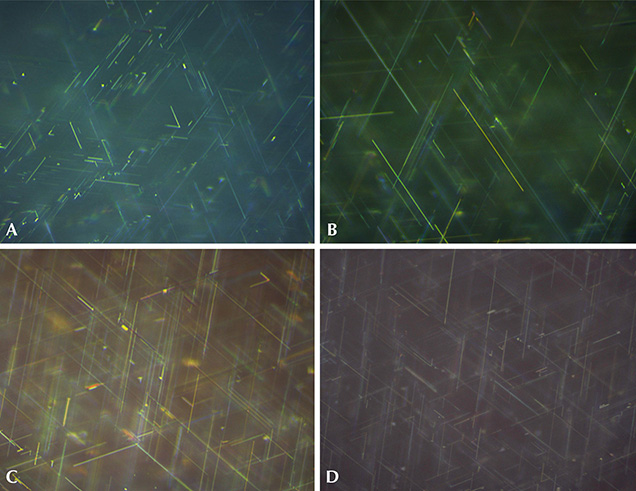
Rutile needles exsolved in Verneuil-grown synthetic star corundum crystals in the form of cylindrical boules, such as the Linde material and samples from other producers, have been shown to exhibit varying lengths, up to a maximum of about 50 µm (Schmetzer et al., 2015). For the six Wiede’s stars studied here, the needle lengths were also variable in each sample, as depicted in figure 10. However, a maximum of approximately 15 µm was reached for one synthetic sapphire (figure 10A; see also figure 1), and maximal lengths between 35 and 45 µm were observed for the other three sapphire cabochons and the two synthetic rubies (figure 10, B and C; see also figure 2, right). The thickness (diameter) of the rutile needles for all six samples was found to be in the range of 0.3 to 0.4 µm. The needle dimensions were always identical at the bases and domes of the cabochons.
At these dimensions, the rutile needles in one blue sapphire were shorter than those observed in any of the other three blue sapphires and the two rubies from Wiede’s production. The rutile needles in this one sample were also noticeably shorter than the rutile precipitates observed, in general, in various types of Linde synthetic rubies and sapphires or in similar samples from other producers (figure 10D). For the other five samples from Wiede’s production, the rutile needles were only moderately shorter than those in Linde samples, or even occasionally in the same range. In terms of thickness, the needles in the Wiede’s cabochons were consistent with those in samples from Linde and other producers.
DISCUSSION AND CONCLUSIONS
The process developed and applied at Wiede’s Carbidwerk for the production of synthetic asteriated rubies and sapphires was invented by Ancot and Eppler in the mid-1950s and used at the company until the end of the 1970s. The samples examined for the present paper likely originated from the 1960s and 1970s, thus representing production later than the first generation described by Eppler (1957/1958, 1958 a,b). Nonetheless, the general principles set forth in the two German patents by Ancot and Eppler (1957a,b) remained valid for the later generations, despite continuous incremental refinements in growth techniques throughout the 1960s and 1970s (C. Schulz and H. Schulz, pers. comm., 2016). The present study has revealed additional details regarding the nature of the methods employed for growth of these materials, augmented by insight from the producer, as described below.
Oriented seeds of synthetic sapphire were seen as small colorless shafts in all rough ruby and sapphire crystals grown by Wiede’s. As confirmed by the producer, without such oriented seeds, the orientation of the synthetic ruby and sapphire crystals would become unpredictable, and, for preparation of asteriated ruby and sapphire cabochons, the center of the star and cabochon dome would need to be found separately for each crystal.
The use of oriented seeds for growing synthetic corundum was first described in a German patent by R. Thilenius (1941) and later in British and U.S. patent documents by M.H. Barnes (1946, 1953) assigned to Linde Air Products Company or Union Carbide and Carbon Corporation (of which Linde had become a division). These patents explained that a small piece or seed of corundum was embedded in a ceramic foot (figure 11). Next,
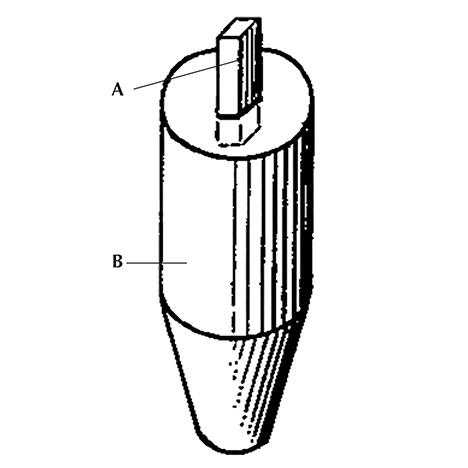
An analogous technique was applied—in general—by Linde for the commercial production of asteriated rubies and sapphires (see the detailed description in the patent by Burdick and Jones, 1954).
The Ancot and Eppler patents dealing with Wiede’s methodology stated that crystal growth started at a lower temperature with an O2:H2 ratio of 40:100 and was slowly raised during the growth process to a higher temperature and a ratio of 49:100. During the initial stages of crystallization and growth of an oriented corundum single crystal, the flame temperature at the melting point needed to be somewhat lower to avoid melting the seed. For subsequent stages, a higher temperature was required to obtain a homogeneous film of melt over the entire surface of the growing crystal (C. Schulz and H. Schulz, pers. comm., 2016). Such details demonstrate how the general principles described by Ancot and Eppler continued to be used for growing the elliptical or almost spherical corundum crystals, while simultaneously showing that the particular temperature-time protocol given in the Ancot and Eppler patent documents could be modified to a certain degree based upon practical experience. Slightly different temperature-time protocols would also presumably have been applied for growing rubies versus sapphires.
The asteriated ruby and sapphire cabochons examined for the present study reflected the just-described process of seeded growth at varying temperatures. This resulted in up to three discernible growth regions. The clear blue or red area in the center of the cabochons, which was previously noted only by Breebaart (1957), represented the zone of the growing crystal around the oriented seed. In this more transparent area, no exsolved rutile needles were observed microscopically in the current study. Within the two other growth zones (i.e., within the less transparent main body of the crystal and the more transparent outer layer or layers), high concentrations of rutile needles were present. However, it should be mentioned that the outermost, more transparent layer could be thinner or completely absent, again as a consequence of the particular temperature-time protocol used. Fashioning could also lead to variations in the zoned appearance. For example, if only the upper half of the spherical boule were used to produce an asteriated cabochon, any transparent regions below would be removed.
Compared to the rutile needles seen in asteriated corundum manufactured by Linde or other Verneuil producers, those examined in the Wiede’s cabochons were generally somewhat shorter in the two rubies and three of the sapphires and distinctly shorter in the fourth sapphire. Eppler (1957/1958, 1958 a,b) had stressed the reduced length of the needles in the Wiede’s stones, but perhaps more than would apply to the material considered in the present study. The increased needle thickness he noted in Wiede’s synthetics was not observed in the present study. Furthermore, the material examined here contained round gas bubbles, which also contrasted with Eppler’s descriptions. Another comment by Eppler that might warrant clarification based on later work is his mention of an absence of Plato striations in the Linde material. Such striations were occasionally found in a recent reexamination of Linde samples (Schmetzer et al., 2015), and hence their presence or absence in a particular stone offers little evidence of the manufacturer. Overall, the difference between Eppler’s observations and ours suggests that the ongoing incremental changes in the manufacturing process used by Wiede’s Carbidwerk from the 1950s through the 1970s also caused somewhat varied microscopic properties and visual appearances.
Eppler (1957/1958, 1958 a,b) concluded that the different dimensions of the rutile precipitates within the host corundum cabochons led to moderately broader arms for the six-rayed stars developed in the Wiede’s synthetics than those normally observed in Linde samples. In addition, he suggested that the broader, less sharp arms tended to result in a more natural-looking gemstone from Wiede’s, as opposed to the typical Linde stars. However, while these observations by Eppler might apply to part of Wiede’s early production, there is little contrast between the visual appearance of the Wiede’s synthetics from the 1960s or 1970s examined here and samples from Linde or other more recent manufacturers (figure 12).
According to the producer, by using the method invented at Wiede’s and patented in the 1950s (or a variant of that process), it is possible to grow stable (non-fragile) ruby and sapphire crystals with even higher titanium concentrations than the upper limit of 0.52 wt.% TiO2 mentioned above. Such samples, however, are more milky white than the intense blue or red colors preferred, thus rendering them unmarketable (C. Schulz and H. Schulz, pers. comm., 2016).